Exploring the Intricacies of the Process of Ultrasonic Weld Fabrication: A Comprehensive Guide
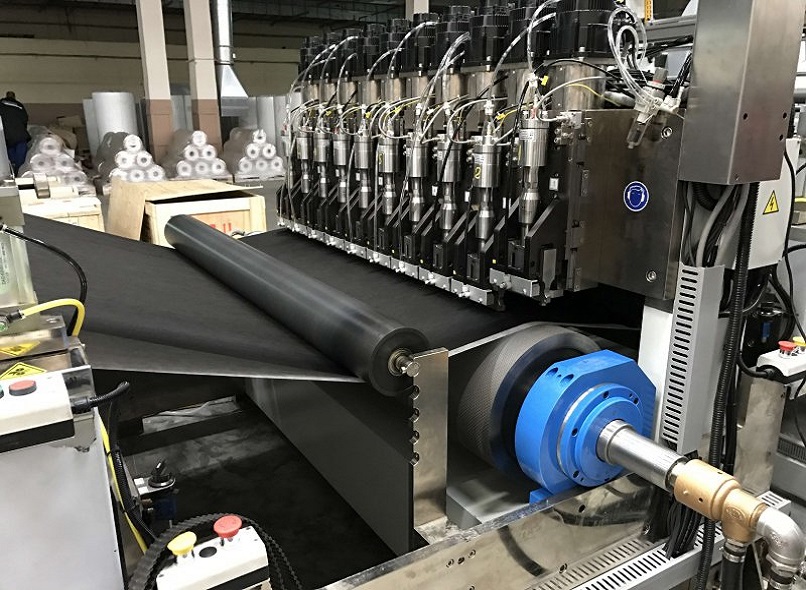
Ultrasonic welding is a highly advanced and widely used technique in the manufacturing industry. It provides a fast, efficient, and reliable method for joining thermoplastic materials, including fabric. In this comprehensive guide, we will delve into the process of ultrasonic weld fabrication, exploring its steps, advantages, applications, and the factors that contribute to successful fabric welding.
Understanding Ultrasonic Weld Fabrication
Ultrasonic weld fabrication refers to the process of utilizing ultrasonic welding technology to join fabric materials together. This technique utilizes high-frequency vibrations to create heat and pressure, which in turn melts the fabric surfaces, resulting in a strong and durable bond. Ultrasonic weld fabrication is particularly suitable for fabrics that cannot be easily sewn, glued, or stitched, providing seamless and robust connections.
The Steps Involved in Ultrasonic Weld Fabrication
The process of ultrasonic weld fabrication consists of several intricate steps, each contributing to the successful joining of fabric materials. These steps include:
- Preparation: Before initiating the welding process, thorough preparation is essential. This involves selecting the appropriate fabric materials and ensuring they are clean, free from contaminants, and properly aligned. Any surface imperfections or irregularities should be addressed to achieve optimal weld quality.
- Assembly: The fabric pieces to be joined are carefully assembled, aligning the edges and surfaces in the desired configuration. Proper alignment is crucial to ensure a strong and seamless weld. Various techniques, such as clamping or adhesive pre-bonding, may be employed to secure the fabric pieces in place prior to welding.
- Ultrasonic Welding Equipment: An ultrasonic welding machine is used for the fabric welding process. The machine consists of a transducer, a booster, and a sonotrode. The transducer converts electrical energy into high-frequency vibrations, which are then amplified by the booster and transmitted to the sonotrode.
- Application of Pressure and Heat: The sonotrode is pressed against the fabric materials with the appropriate amount of force, ensuring proper contact and alignment. Simultaneously, high-frequency vibrations are applied to the sonotrode, generating friction and heat. The heat softens the fabric surfaces and initiates the melting process.
- Melting and Bonding: As the fabric surfaces melt, they fuse together to form a strong and durable bond. The melted material flows and intermingles, creating a solid connection between the fabric pieces. The duration of the welding process depends on factors such as the type and thickness of the fabric materials.
- Cooling and Solidification: Once the desired welding time has elapsed, the heat is removed, allowing the melted fabric to cool and solidify. This stage is crucial for the bond to become strong and stable, ensuring the integrity and longevity of the joined fabric pieces.
- Inspection and Finishing: After the weld has cooled down, it undergoes thorough inspection for quality and strength. Any excess material or imperfections are trimmed or removed, resulting in a neat and finished appearance. The welded fabric can then be subjected to further processing or assembly as required.
Advantages of Ultrasonic Weld Fabrication
Ultrasonic weld fabrication offers several advantages over traditional fabric joining methods:
- Speed and Efficiency: Ultrasonic welding is a fast process, enabling high-volume production. It eliminates the need for additional adhesives, stitches, or fasteners, saving time and labor.
- Strong and Durable Bonds: The ultrasonic weld fabrication technique creates robust and reliable bonds that withstand various mechanical stresses. The welded seams are typically as strong as the fabric material itself, ensuring excellent performance and longevity.
- Aesthetic Appeal: Ultrasonic weld fabrication leaves minimal visible marks on the fabric surface, resulting in a clean and aesthetically pleasing finish. This is particularly advantageous for applications where a seamless appearance is desired.
- Versatility: Ultrasonic welding can be used with a wide range of fabric materials, including synthetic fabrics, natural fibers, and blends. It is suitable for joining different fabric thicknesses and shapes, providing flexibility in design and manufacturing.
- Enhanced Productivity: Ultrasonic weld fabrication allows for high-speed production, reducing manufacturing time and increasing productivity. It also eliminates the need for additional processing steps, such as sewing or gluing, streamlining the production process.
- Environmental Friendliness: Ultrasonic weld fabrication is a greener alternative to traditional fabric joining methods that may involve the use of adhesives or solvents. It eliminates the need for additional chemicals, reducing the environmental impact of the manufacturing process.
Applications of Ultrasonic Weld Fabrication
Ultrasonic weld fabrication finds applications in various industries and sectors, including:
- Automotive: Ultrasonic weld fabrication is used in the automotive industry for joining fabric components such as seat covers, headliners, and interior trims. It provides strong and durable connections, ensuring the longevity and quality of automotive interiors.
- Textile: The textile industry utilizes ultrasonic weld fabrication for applications such as garment manufacturing, fabric assembly, and textile product development. It enables the creation of seamless and durable fabric connections, enhancing the overall quality of textile products.
- Medical: In the medical field, ultrasonic weld fabrication is employed in the production of medical textiles, including surgical gowns, drapes, and protective clothing. The strong and reliable bond created by ultrasonic welding ensures the integrity and effectiveness of these critical medical garments.
- Technical Textiles: Ultrasonic weld fabrication is also utilized in the manufacturing of technical textiles, such as airbags, filters, and geotextiles. It provides a reliable and efficient method for joining specialized fabric materials used in demanding applications.
- Outdoor Gear: Ultrasonic weld fabrication is commonly used in the production of outdoor gear, including tents, backpacks, and protective clothing. The strong and waterproof connections achieved through ultrasonic welding ensure the durability and performance of these outdoor products.
- Electronics: Ultrasonic weld fabrication is employed in the electronics industry for joining fabric components used in electronic devices, such as flexible circuits and wearable technology. It provides a reliable and efficient method for creating connections that can withstand the demands of electronic applications.
Factors Affecting Successful Fabric Welding
Several factors contribute to the success of ultrasonic weld fabrication for fabric materials:
- Fabric Selection: The type, composition, and thickness of the fabric materials play a significant role in the weld quality. Different fabrics have varying melting points and behaviors when subjected to heat and pressure. Understanding the fabric properties is crucial for achieving optimal weld results.
- Welding Parameters: The welding parameters, including the amplitude, frequency, pressure, and duration, need to be carefully selected and optimized for the specific fabric materials. Fine-tuning these parameters ensures a strong and reliable bond while minimizing any potential damage to the fabric.
- Surface Preparation: Proper surface preparation, including cleaning and alignment, is essential for achieving a successful weld. Any contaminants or irregularities on the fabric surfaces can negatively affect the weld quality. Thorough cleaning and alignment are crucial for optimal fabric joining.
- Equipment Maintenance: Regular maintenance and calibration of the ultrasonic welding equipment are vital to ensure consistent and reliable weld results. Properly maintained equipment ensures accurate control of welding parameters and reduces the risk of process variations.
- Expertise and Training: Skilled operators and technicians with expertise in ultrasonic welding techniques are essential for achieving high-quality fabric welds. Proper training ensures that the operators understand the process, equipment operation, and troubleshooting techniques, resulting in consistent and reliable welds.
Conclusion
Ultrasonic weld fabrication is a highly effective and versatile method for joining fabric materials. It offers numerous advantages, including speed, strength, aesthetics, versatility, enhanced productivity, and environmental friendliness. By understanding the intricacies of the process, applications, and factors affecting successful fabric welding, manufacturers and designers can leverage this technology to achieve seamless, durable, and high-quality fabric connections in various industries. Embracing the power of ultrasonic weld fabrication opens up new possibilities for innovation and advancement in fabric manufacturing and product development.
See more ultrasonic welders