Discovering the Intricacies of Ultrasonic Welding Copper: A Comprehensive Guide
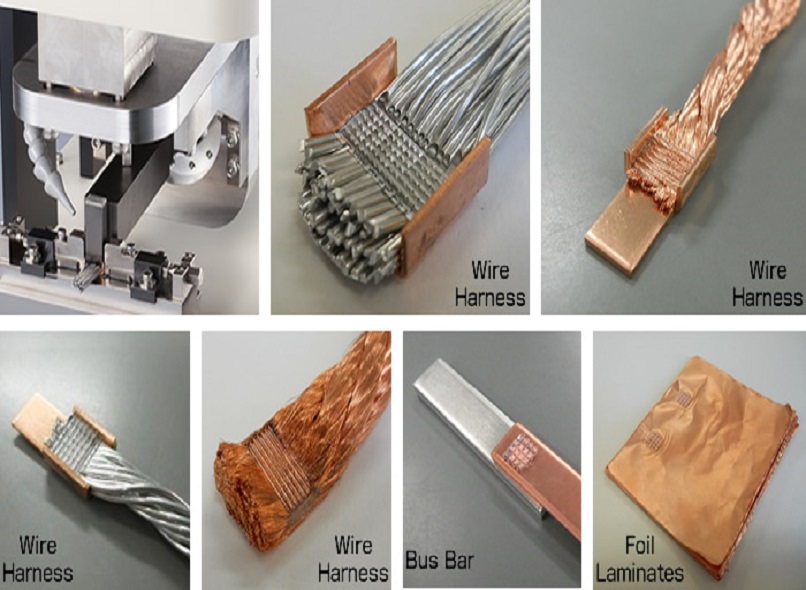
Ultrasonic welding has emerged as a groundbreaking technique in the realm of metal joining, enabling the seamless fusion of various metals, including copper. This article aims to provide a comprehensive exploration of the intricate process behind ultrasonic welding copper, unraveling each step and shedding light on its underlying principles and applications.
Introduction to Ultrasonic Welding
Ultrasonic welding serves as a solid-state joining process, harnessing the power of high-frequency ultrasonic vibrations to create robust and durable bonds between metal surfaces. Its exceptional suitability for copper arises from the metal's remarkable electrical conductivity, thermal conductivity, and corrosion resistance. By leveraging ultrasonic vibrations, manufacturers can achieve flawless connections in copper components, ranging from electrical connectors and heat exchangers to intricate electronic circuitry.
Step 1: Preparation - The Cornerstone of Success
The journey towards a successful weld commences with meticulous preparation. Thoroughly cleansing the copper surfaces and eliminating any contaminants that might hinder the welding process lays the foundation for a flawless ultrasonic weld. Employing an appropriate cleaning agent and ensuring impeccable surface conditions are paramount in achieving optimal results.
Step 2: Assembly - Precision and Alignment for Seamless Integration
Once the copper surfaces are immaculately clean, the subsequent step involves aligning and assembling the copper pieces to be joined. Precision and alignment play a pivotal role in guaranteeing a reliable and resilient weld. Accurate alignment ensures optimal contact between the copper surfaces, facilitating the seamless transmission of ultrasonic vibrations and enabling the formation of a strong and enduring bond.
Step 3: Clamping - Stabilizing the Connection for Unwavering Performance
To maintain alignment and contact between the copper components throughout the welding process, proper clamping is indispensable. Utilizing a suitable fixture or tool, the copper pieces are securely clamped together, effectively preventing any unintended movement or separation during the application of ultrasonic vibrations. This ensures a stable and controlled environment for the welding procedure.
Step 4: Ultrasonic Welding - Channeling the Power of Vibrations
At the heart of the ultrasonic welding process lies the application of high-frequency vibrations. A transducer generates these ultrasonic vibrations, typically ranging from 20 kHz to 70 kHz. These vibrations are then transmitted to the copper surfaces through a sonotrode or horn. As the sonotrode makes contact with the copper surfaces, friction and localized heating occur at the interface, initiating the welding process.
Step 5: Bond Formation - The Fusion of Copper Surfaces
Under the influence of the ultrasonic vibrations and the applied pressure, the copper surfaces experience localized heating. This heating causes the copper material to soften and flow, facilitating the formation of a metallurgical bond. The combination of heat, pressure, and molecular diffusion at the interface results in a strong and enduring joint between the copper pieces, ensuring long-lasting performance.
Step 6: Cooling and Solidification - Fortifying Strength and Integrity
Upon completion of the bond formation, the ultrasonic vibrations and pressure cease, allowing the welded copper parts to cool naturally. This controlled cooling period enables the solidification of the molten copper material, reinforcing the strength and integrity of the joint. By carefully managing the cooling process, manufacturers minimize the potential for distortion or other undesirable effects, ensuring the reliability of the welded copper components.
Step 7: Post-Weld Inspection - Ensuring Excellence and Reliability
Once the welded copper joint has completely cooled down, conducting a thorough post-weld inspection becomes imperative. This inspection aims to verify the quality and integrity of the weld, ensuring it meets the required standards and specifications. Various non-destructive testing methods, including visual inspection, ultrasonic testing, or radiographic examination, can be employed to assess the soundness of the weld, ensuring the utmost quality and reliability of the final product.
Conclusion
Ultrasonic welding stands as a versatile and efficient method for joining copper components, offering an array of advantages, including rapid welding speed, exceptional weld strength, and minimal distortion. By comprehending the intricacies of the ultrasonic welding process and meticulously following the step-by-step procedure, manufacturers can harness this remarkable technique to create reliable and durable connections in copper. Whether in the realm of electronics, automotive, or any other industry relying on copper's exceptional properties, ultrasonic welding remains a steadfast and effective solution, paving the way for innovative advancements and ensuring the seamless integration of copper components.