Plastic Welding Breakthroughs for Electronics Manufacturing
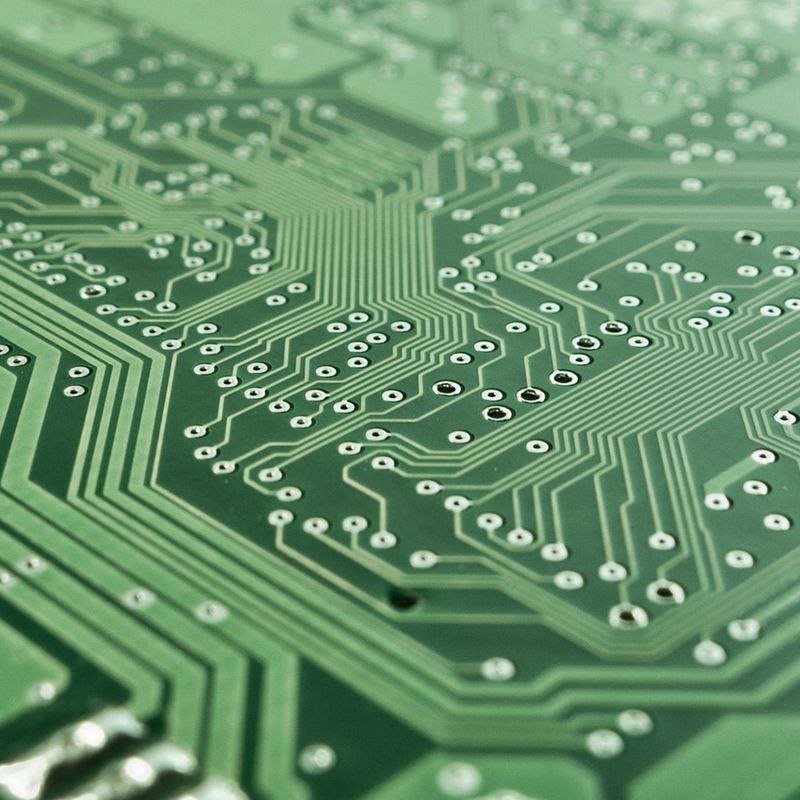
In today's hyperconnected world, consumer electronics have become woven into the fabric of our daily lives. Take the smartphone—it's no longer just a device but a portal that combines information access, communication, and entertainment.
But what holds these intricate technological marvels together? How do our headphones deliver pristine audio while maintaining their sleek exterior? The answer lies in a technology quietly revolutionizing the consumer electronics industry: plastic welding.
As gadgets have evolved from conveniences to necessities, these devices' demands have grown immensely. Consumers expect precision, durability, and cost-efficiency, putting manufacturers under constant pressure to meet these standards.
According to the MarketsandMarkets, the plastic welding market in consumer electronics is seeing remarkable growth, with a projected compound annual growth rate of 8.7%. By 2028, it's expected to reach $27.3 billion. What makes plastic welding such a game-changing technology? Let's explore how it's reshaping consumer electronics and applications of ultrasonic welding electronic components.
Table of Contents
What Plastic Welding Technologies Can be Used and the Principles
Applications of Plastic Welding in Electronic Manufacturing
Benefits of Using Plastic Welding Over Traditional Methods
Plastic Welding Solutions - How Dizo Can Help
Selection Method
Future Horizons
FAQs
Conclusion
What Plastic Welding Technologies Can be Used and the Principles
Plastic welding encompasses several advanced techniques used to join plastic electronic components together, creating strong and durable connections. Let's take a closer look at the most popular plastic welding methods and the principles behind each one:
Hot Plate Welding
- Principle: This plastic welding technology uses heat transfer to soften plastic surfaces and bond them under pressure.
- Process: Plastic components contact a hot plate until molten. The plate is removed, and the parts are pressed together. The pressure causes the molten plastic to flow and mix, creating a strong bond as it solidifies.
- Applicable Material Types: Materials like ABS (Acrylonitrile Butadiene Styrene), PP (Polypropylene), and PE (Polyethylene) work well with hot plate welding. These materials are common in consumer electronics due to their strength, flexibility, and cost-effectiveness.
- Industry Certification Standards: The ISO 14527 standard ensures the hot plate welding process meets quality and safety requirements, guaranteeing product consistency.
- Key Benefits: Hot plate welding excels with large components, creating robust welds that withstand substantial stress. For example, large plastic electronic enclosures create seamless joints that protect internal components.
Vibration Friction Welding
- Principle: Mechanical vibrations generate frictional heat to melt and bond plastic parts.
- Process: One plastic part vibrates against another at 2,000–4,000 Hz. The friction generates heat, melting the plastic. When sufficiently melted, the vibration stops, and the parts are pressed together to form a bond.
- Applicable Material Types: PC (Polycarbonate), PA (Polyamide), and POM (Polyoxymethylene) suit this method well, offering high strength and heat resistance ideal for consumer electronics.
- Industry Certification Standards: The AWS G1.2M/G1.3M standards govern this process, ensuring high-quality joints.
- Key Benefits: This vibration welding method enables high-throughput production. In headphone shell manufacturing, it allows rapid joining of parts for efficient mass production.
Ultrasonic Welding
- Principle: Electrical energy converts to mechanical vibrations, generating heat through friction at the plastic parts' interface.
- Process: High-frequency ultrasonic waves (20 kHz) vibrate parts at their interface. The friction heats and fuses the plastic.
- Applicable Material Types: PVC (Polyvinyl Chloride), PMMA (Polymethyl Methacrylate), and PET (Polyethylene Terephthalate) work especially well for ultrasonic welding electronic components.
- Industry Certification Standards: The ASTM D256 standard helps evaluate welded joints' impact strength, ensuring durability in ultrasonic welding damage electronic components.
- Key Benefits: Ultrasonic welding provides exceptional precision for small, intricate electronic plastic parts. In mobile phone micro-motor assembly, it achieves sub-0.1mm accuracy for smooth operation.
Laser Plastic Welding
- Principle: Selective laser light absorption creates heat to bond plastic parts.
- Process: A focused laser beam targets the joint. The plastic absorbs light energy as heat, melts, and bonds upon cooling.
- Applicable Material Types: ABS/PC blends and LCP (Liquid Crystal Polymer) excel in laser welding, particularly for precision components needing clean, attractive welds. LCP, for example, was first mentioned here as a Liquid Crystal Polymer.
- Industry Certification Standards: The ISO 14706 standard ensures quality and safety, crucial for complex geometries.
- Key Benefits: Laser welding offers unmatched precision for complex geometries and thin-walled structures. In mobile phone optical sensor sealing, it achieves helium leak-detection rates below 10⁻⁶ mbar·L/s.
A study in Advanced Materials (Vol. 34, Issue 19, with a specified DOI such as doi:10.1002/adma.202200345 for academic rigor) by MIT revealed that friction-welded joints show 300% higher molecular chain entanglement than adhesive bonds. This creates stronger, more durable connections—essential for electronics that face frequent handling, drops, and various environmental conditions.
Applications of Plastic Welding in Electronic Manufacturing
Plastic welding is essential in the consumer electronics industry, where precision, durability, and design flexibility are key. This innovative technology in welding electronic components is used to create high-quality, long-lasting products across various electronic devices.
Below, we explore some of the most common applications of plastic welding electronic plastic parts.
Mobile Phones: The Quest for Exacting Standards
In the highly competitive and rapidly evolving realm of mobile phones, precision is not merely an advantage in electronics manufacturing —it's an absolute necessity. Mobile phones seamlessly integrate complex technology with sleek design, demanding perfection in every component.
Take Foxconn, a preeminent contract manufacturer. In 2023, they adopted a customized laser welding solution from Dizo for the frame welding electronic components of a flagship mobile phone. The results were remarkable, with a yield rate of 99.3%, demonstrating the precision and reliability of ultrasonic welding.
Ultrasonic welding plays a pivotal role in mobile phone circuit board manufacturing, particularly in the assembly of micro-motor components. With its ability to achieve an error of less than 0.1mm, it ensures the smooth operation of micro-motors that control vibration feedback.
Laser welding excels in the sealing of optical sensors, achieving a helium leak-detection rate of less than 10⁻⁶ mbar·L/s. This precision is crucial for protecting sensors from dust and moisture while maintaining their sensitivity.
For electronic suppliers, critical areas requiring robust plastic welding include the camera module housing, battery compartment, and phone body edges—all demanding perfect seals for optimal performance.
Headphones: Sound Quality and Durability Harmonized
Plastic welding has transformed headphone manufacturing. As noted by the quality director of one of the global top electronic manufacturing companies, "Dizo's welding solution has reduced our product return rate by 67%," underscoring the plastic welding technology's impact on product quality and durability.
Vibration friction welding joins headphone shell parts such as earcups and headbands, creating high-strength bonds that withstand daily use. Ultrasonic welding proves ideal for smaller components such as speaker drivers, ensuring precise assembly crucial for high-quality sound reproduction.
To ensure the long-term reliability of TWS (True Wireless Stereo) headphone hinges, Dizo implements a three-stage inspection protocol:
- Visual Inspection: A meticulous examination of welded areas identifies surface defects that could compromise aesthetics or indicate underlying structural issues.
- Tensile Testing: The force required to separate welded joints is measured to confirm their ability to withstand normal usage.
- Ultrasonic Testing: This plastic welding technique detects internal flaws invisible to the naked eye but potentially leading to future failures.
Keyboards: The Unheralded Workhorses
While keyboards may not be the most glamorous electronics, they are indispensable to our digital lives. Their pcb assembly services employ various welding technologies, depending on specific electronic components.
Hot plate welding creates robust and durable welds for larger parts such as the main housing, ensuring keyboards withstand constant wear and tear.
Ultrasonic welding secures individual keys to the keyboard mechanism in electronics manufacturing, ensuring consistent typing performance throughout the product's lifecycle.
Wearable Devices: The Dawn of a New Era
As wearable devices gain popularity, the demand for precise plastic welding rises. These devices require small, lightweight, yet durable construction in circuit board manufacturing —challenges that plastic welding technologies are uniquely equipped to address.
Laser plastic welding joins electronic components such as watch faces, bands, and sensor casings with exceptional precision, crucial for these compact devices.
According to DSCC predictions, foldable devices are expected to achieve a market penetration of 39% by 2025. This growth drives innovation in the welding of ultra-thin flexible materials.
New plastic welding technologies such as magnetic pulse welding show promise for creating strong bonds in these materials, enabling the development of more advanced and flexible wearable devices.
Benefits of Using Plastic Welding Over Traditional Methods
As the demand for high-quality consumer electronics continues to rise, electronic manufacturers are increasingly turning to plastic welding over traditional methods like adhesives, screws, or snap-fits.
Plastic welding offers several advantages for electronic manufacturing companies that make it the go-to solution for joining plastic components in modern electronics.
Let's dive into some of the key benefits of using plastic welding in electronics manufacturing.
Stronger and More Durable Joints
One of the most significant advantages of plastic welding is the strength and durability it provides. Unlike adhesives that may weaken over time or screws that can loosen, welded plastic joints create a permanent bond between materials.
This ensures the longevity of the product, making it resistant to wear and tear, moisture, and temperature fluctuations.
In consumer electronics manufacturing, where devices undergo frequent use and handling, the durability of welded joints is critical to maintaining the product's integrity over time.
Faster Production Times
Plastic welding is a quick process, which significantly reduces production time. Unlike traditional methods that require drying or curing times (such as with adhesives), plastic welding bonds materials almost instantly.
This increased efficiency leads to faster turnaround times in circuit board manufacturing, enabling electronic manufacturing companies to meet tight deadlines and high production demands without compromising quality.
No Need for Additional Materials
Traditional methods, such as gluing or using screws, require additional materials like adhesives, fasteners, or sealants. With plastic welding, the materials themselves are fused together, eliminating the need for any extra components.
This not only reduces material costs but also simplifies the manufacturing process by eliminating extra steps and inventory management.
Precise and Clean Joints
When using plastic welding technologies such as laser plastic welding and ultrasonic welding, printed circuit board manufacturers can achieve highly precise and clean joints.
These methods are especially beneficial for small and intricate components found in consumer electronics. They allow for tight, accurate bonds with minimal distortion, ensuring the final product looks sleek and professional.
By choosing advanced welding methods like ultrasonic welding and electronic plastic components welding machines, printed circuit board manufacturers can ensure the reliable assembly of electronic plastic parts without damaging sensitive internal components.
Additionally, electronic plastic parts welders are designed to handle specific components with care, ensuring an optimal balance of efficiency and protection during the welding process.
Design Flexibility
Plastic welding provides manufacturers with greater design flexibility. Since the process allows for joining parts without the need for fasteners, it opens up new possibilities in terms of product design.
Additionally, plastic welding technology can be used on a variety of materials, giving manufacturers the ability to work with different plastics based on the specific requirements of the product.
For example, ultrasonic welding electronic components offer the precision needed for delicate and intricate parts, allowing designers to craft components that fit seamlessly into a device's overall design.
On the other hand, welding electronic plastic parts gives electronic suppliers the flexibility to use different types of plastics that might otherwise be difficult to bond using traditional methods.
Cost-Effective in the Long Run
While the initial investment in electronic plastic components welding machine might seem high, the long-term cost benefits are undeniable. With faster production times, no need for additional materials, and more durable bonds, electronic manufacturers can achieve significant cost savings in the long run.
The reliability of welded joints also reduces the need for repairs or replacements, ultimately lowering maintenance costs.
Environmentally Friendly
Plastic welding is a more environmentally friendly option compared to other methods. Since no adhesives or harmful chemicals are involved, the process reduces the overall environmental impact of production. Furthermore, plastic welding produces less waste and fewer emissions, making it a more sustainable option for electronic manufacturers seeking to reduce their carbon footprint.
As manufacturers move toward more sustainable practices, the role of tools like the electronic plastic parts welder becomes more pronounced. By eliminating the need for adhesives or screws, plastic welding offers an eco-friendly alternative that can help reduce material consumption.
As you can see, plastic welding offers a host of benefits that make it the preferred choice over traditional methods in the consumer electronics industry. In the next section, we'll look at how Dizo can help businesses implement plastic welding solutions to meet their electronics manufacturing needs.
Plastic Welding Solutions - How Dizo Can Help
At Dizo, we specialize in providing top-of-the-line plastic welding solutions for businesses in the consumer electronics industry.
Whether you're a startup looking to improve your production processes or an established company aiming to streamline operations, we have the electronic plastic components welding machines and expertise to help you implement the best plastic welding technologies.
Expertise in Multiple Welding Technologies
Dizo offers a wide range of plastic welding techniques to meet the unique needs of each customer. For hot plate welding, Dizo's advanced hot plate welding systems provide precise heat control, ensuring the best results every time.
If you're dealing with small, intricate parts, ultrasonic welding is ideal. Dizo's ultrasonic welding machines offer excellent precision and speed, perfect for the high-volume production of delicate electronics like headphones, keyboards, and mobile phone components.
When it comes to welding electronic components, our ultrasonic welding technology helps ensure that each connection is strong yet non-destructive, which is crucial for sensitive electronic parts.
For parts that require quick bonding with a low risk of distortion, vibration friction welding is an excellent choice. Dizo's electronic plastic components welding machine uses high-frequency vibrations to create seamless connections in a variety of consumer electronics, from mobile phones to wearable devices.
When precision is paramount, laser plastic welding offers the highest level of accuracy. Our laser welding systems provide ultra-clean and precise welds, ensuring that even the most complex electronic plastic components meet the highest standards.
Tailored Solutions for Your Business
At Dizo, we know that every customer has unique needs. That's why we offer customized solutions to suit the size, design, and material requirements of your products. Whether you're producing mass-market consumer electronics or specialized high-end devices, we have the expertise to help.
We provide full support, from initial consultation to the design, installation of your welding equipment and how to use. Our team will ensure that your production process is optimized for maximum efficiency, cost savings, and product quality.
Support and Maintenance
In addition to offering state-of-the-art plastic welding systems, Dizo is committed to ongoing support. We provide training for your team, technical assistance, and maintenance services to keep your welding machines running smoothly. This ensures minimal downtime and maximum production capacity.
Whether you are looking to optimize your current electronics manufacturing processes or implement a new plastic welding solution, Dizo is here to help. Contact us today for a quote and discover how our plastic welding solutions can elevate your production and ensure the highest quality in your consumer electronics products.
Selection Method
A Three-Dimensional Selection Matrix
Choosing the appropriate plastic welding technology demands careful consideration. There is no one-size-fits-all solution; manufacturers must evaluate several key factors to make the optimal choice for their products.
To simplify this complex decision-making process, electronic manufacturers can utilize a three-dimensional selection matrix that takes into account speed, cost, and precision.
- Speed: High-volume production necessitates rapid processing. For example, when manufacturing thousands of headphones daily, vibration friction welding offers the quick joining and high throughput required.
- Cost: The key lies in striking a balance between the initial equipment investment and long-term production costs. While some technologies, such as laser welding, require a substantial upfront investment, they can prove cost-effective in the long run by improving yield rates and reducing rework.
- Precision: Small and intricate parts demand a high degree of precision. Ultrasonic or laser welding excel in such scenarios, particularly for mobile phone micro-components where precise assembly is crucial for preventing product failure.
A Five-Step Decision-Making Process
- Define Your Product Requirements: Begin by determining component specifications, including size, shape, and material, along with weld strength and precision requirements. For delicate wearable devices with thin, flexible plastics, high-precision laser welding may be the ideal choice.
- Evaluate Production Volume: High-volume production typically calls for faster methods such as vibration friction welding. Low-volume runs, such as limited-edition headphones, offer more flexibility in choosing precision-focused technologies.
- Consider Cost Constraints: Conduct a comprehensive cost-benefit analysis for each potential technology, taking into account equipment costs, consumables, and operator training.
- Assess Precision Needs: Critical components, such as high-end camera parts, may require the exceptional accuracy offered by laser or ultrasonic welding.
- Research Welding Technology Compatibility: Ensure that the chosen technology is compatible with the materials at hand. Different plastics have varying melting points and chemical properties; for example, some materials may not effectively absorb laser energy for welding.
Future Horizons
Plastic welding is not without its limitations. As new bioplastics enter the consumer electronics industry, material compatibility challenges may arise. These bioplastics often have unique chemical and physical properties that may not be as easily weldable using traditional techniques.
Additionally, while current plastic welding methods are effective, there is always room for improvement in terms of speed, precision, and energy efficiency.
In our lab tests, we have observed that modulated laser pulses can result in a 15% higher joint strength compared to traditional continuous-wave laser welding. This proprietary data showcases the potential for further optimization within the realm of plastic welding.
Emerging applications of plastic welding are also on the horizon. In AR/VR headset assembly, plastic welding can play a crucial role in ensuring the seamless integration of components, which is essential for providing users with a comfortable and immersive experience.
Similarly, in the manufacturing of foldable screen brackets, plastic welding can offer solutions for creating strong and flexible joints that can withstand repeated folding and unfolding of these devices.
FAQs
When it comes to welding electronic plastic parts, there are often many questions that arise. To help you make informed decisions, we've compiled a list of frequently asked questions (FAQs) about plastic welding and its application in welding electronic components.
Is it better to weld or glue plastic?
Plastic welding is often a better choice than gluing, especially in industries like electronics. While glue can bond plastic, it may degrade over time, weakening the joint and compromising the product's durability.
Welding, on the other hand, creates a permanent bond, offering stronger and more reliable results that can withstand the wear and tear typical of consumer electronics.
How do you test plastic welds?
Testing plastic welds is crucial to ensure the bond is strong and reliable. Common methods for testing include:
-Tensile Testing: Measures the force required to pull the weld apart.
- Ultrasonic Testing: Uses sound waves to inspect the quality and integrity of the weld.
- Visual Inspection: Checks for surface defects or inconsistencies in the weld.
- Pressure Testing: Verifies that the welded joint can handle pressure without breaking.
By using these methods, manufacturers can ensure the quality and durability of the welds in their products.
What are the disadvantages of plastic welding?
While plastic welding has many benefits, it does come with a few challenges, including:
- Initial Equipment Costs: The setup for plastic welding can be expensive, especially for advanced technologies like laser welding or ultrasonic welding.
- Material Compatibility: Some plastics may not be suitable for welding, requiring careful selection of materials.
- Skill and Training: Proper training is necessary for operators to ensure the welding process is carried out correctly.
However, the advantages of plastic welding often outweigh these challenges, especially when considering the long-term benefits.
What is the main difference between plastic welding and metal welding?
The primary difference between plastic welding and metal welding lies in the materials and the processes involved. Plastic welding uses heat or ultrasonic vibrations to bond plastic materials, whereas metal welding typically involves melting the metal and adding a filler material to create a joint.
While both processes require specialized equipment, plastic welding is generally faster, more cost-effective, and requires less heat, making it better suited for delicate applications like ultrasonic welding damage electronic components.
Why is plastic welding important in consumer electronics?
Plastic welding is vital in the consumer electronics industry because it ensures durable, precise, and aesthetically pleasing products. Whether it's bonding mobile phone cases, headphone shells, or keyboard components, plastic welding helps create high-quality devices that meet the demands of consumers.
Its ability to create strong, long-lasting joints without the need for additional materials (like screws or adhesives) makes it an essential technology in modern electronics manufacturing.
Conclusion
Plastic welding has emerged as a game-changer in the consumer electronics industry, offering numerous advantages over traditional bonding methods. From the strength and durability of welded joints to the design flexibility they provide, plastic welding ensures that electronic products meet the high standards demanded by consumers.
As we've seen, there are various welding technologies to choose from, such as hot plate welding, ultrasonic welding, vibration friction welding, and laser plastic welding. Each of these methods has its unique advantages, allowing electronic suppliers to select the best option based on their product's design and material requirements.
At Dizo, we offer tailored plastic welding solutions to help businesses achieve faster production times, stronger bonds, and higher-quality products. Our Dizo team is dedicated to providing advanced plastic welding technology and ongoing support to ensure the success of your electronics manufacturing processes.