Why Choose Servo Heat Staking for Automotive Door Panels?
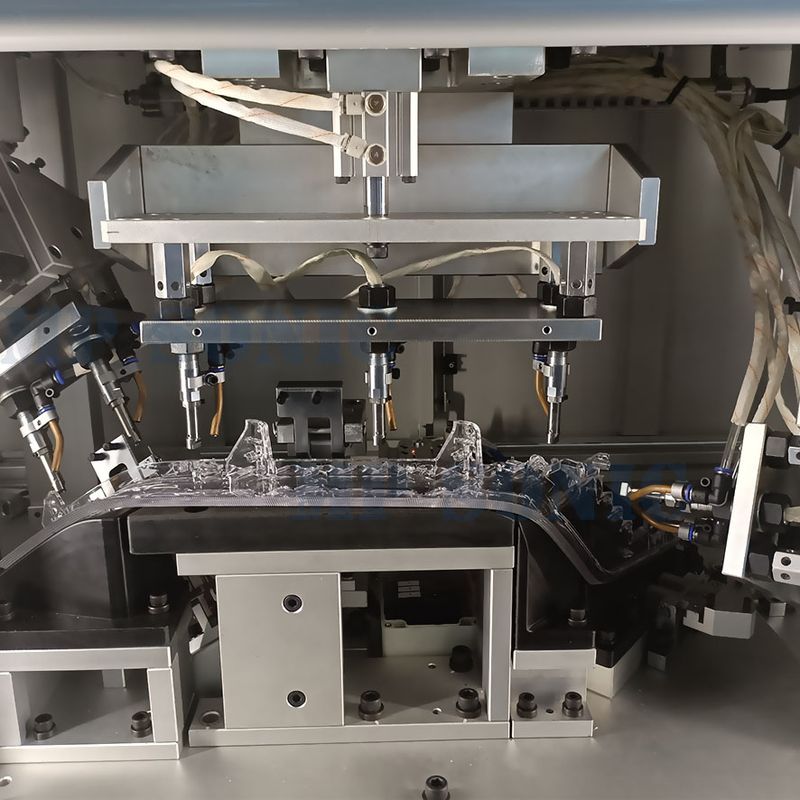
Car manufacturing has come a long way since the 1980s, transforming how vehicles are built. In today's automotive industry, high-quality parts aren't optional; they're essential. Take car door panels, for example. Building durable, reliable panels requires precision and attention to detail because every component matters.
So, how do manufacturers get it right? That's where servo heat staking comes in. This accurate and efficient technology is revolutionizing the production of car door panels.
Servo Heat Staking Machine
Even small errors in door panels can lead to weak joints or uneven finishes, affecting a vehicle's quality. A reliable servo hot staking machine prevents these issues by providing precise control and consistent results. Choosing the right car door panel servo heat staking machine ensures a smooth, efficient process and durable, high-quality panels every time.
Let's take a look at why it is important to choose servo heat staking for automotive door panels!
Table of Contents
What is Servo Heat Staking?
How Does the Heat Staking Process Work?
Difference Between Servo Staking Machines and Traditional Heat Staking
Benefits of Choosing Servo Heat Staking for Automotive Door Panels
Applications Beyond Car Door Panels
How it Aligns with Industry Standards and Sustainability
The Bottom Line
FAQs
What is Servo Heat Staking?
Servo heat staking represents an advanced manufacturing procedure for joining plastic materials with both precise and reliable outcomes. Servo hot staking differs from traditional methods through its use of servo motors to operate heating along with pressure functions and machine movements throughout bonding operations.
Servo heat plastic staking has become a standard technology for industries that need precise mechanical joints, such as automotive production, electronics manufacturing, and aerospace manufacturing.
How Does the Heat Staking Process Work?
Servo heat staking represents an exact technique for manufacturing plastic component assemblies within automotive and electronic sector operations. Servo hot plastic staking follows these specific steps for its operation:
Preparation:
The servo-controlled heat staking equipment positions plastic components that need joining, including a car door panel combined with its trim. Plastic split represents the main aspect where heat generates a bond.
Heating & Application:
A particular heated tool designed with servo motors adjusts its position to touch plastic bosses with high precision. This heat staking tool from your reliable heat staking machine manufacturer, Dizo reaches its temperature at a specific level to enable plastic softening while avoiding any burning damage.
Servo motors perform superior controlled pressure applications instead of using traditional pneumatic systems when working with softened plastic.
Forming the Bond:
While the plastic material is softened, the servo heat staking machine employs a specific shaping method (flattening or flaring) to encase the mating component.
The hot staking machine removes itself from the plastic while simultaneously cooling the softened material, which forms a tough, vibration-proof connection.
Servo Advantages:
Servo motors run automatic checks on the force together with speed and temperature settings during all heat staking process stages.
Difference Between Servo Staking Machines and Traditional Heat Staking
Here are the key differences between making car door panels through Heat staking Machines and traditional machines:
Aspect |
Servo Heat Staking |
Traditional Heat Staking |
Precision & Control |
Uses servo motors for programmable, real-time adjustments to pressure, speed, and temperature. Ensures micron-level accuracy and consistent joint quality. |
Relies on pneumatic/hydraulic systems with fixed parameters. Prone to pressure fluctuations and wear, leading to variability in results. |
Energy Efficiency |
Operates only during active cycles, reducing energy consumption by 20–30%. |
Requires continuous air supply or hydraulic pressure, leading to higher energy waste. |
Flexibility |
Adapts to complex geometries and diverse materials (e.g., thermoplastics, composites) via programmable settings. |
Limited to simpler designs due to rigid mechanical systems. Struggles with intricate or multi-material joints. |
Defect Rates |
Minimizes defects (e.g., weak bonds, over-deformation) through precise control. |
Higher risk of defects due to inconsistent pressure and temperature management. |
Setup & Maintenance |
Quick setup with digital interfaces; lower maintenance due to fewer moving parts. |
Longer setup times; frequent maintenance required for pneumatic seals and mechanical components. |
Cost |
Higher upfront investment but lower long-term costs (reduced scrap, energy, downtime). |
Lower initial cost but higher operational expenses (energy, maintenance, rework). |
Applications |
Ideal for high-precision industries: automotive interiors, medical devices, and electronics. |
Suited for bulkier, non-critical parts (e.g., household appliances, basic automotive components). |
Benefits of Choosing Servo Heat Staking for Automotive Door Panels
Servo heat staking ensures precise and durable assembly for BYD car door panels, meeting the highest quality standards.
By using this advanced technology, manufacturers can reliably meet industry standards and increase customer satisfaction. So why choose servo heat staking machine for automotive door panels? Here are some key benefits to consider:
1. Increased Energy Efficiency
The primary energy-saving capability of servo heat staking strongly differentiates it from other production techniques. The system's negativity impacts energy efficiency. Energy consumption through servo motors takes place exclusively during active heat control pressing operations and cooling stages.
The servo system consumes minimal energy when it stands idle since compressed air in pneumatic systems runs constantly. Exact heat delivery through advanced temperature control systems avoids wasting energy during the process.
Components tend to experience excessive heating when users apply traditional methods, and cycles often need to be longer. Here is a brief breakdown to understand and compare energy consumption:
Aspect |
Servo Heat Staking |
Traditional Heat Staking |
Energy Source |
Electric servo motors (on-demand) |
Pneumatic/hydraulic systems (constant air pressure) |
Idle Energy Use |
Near-zero |
High (compressors run continuously) |
Heat Loss |
Minimal (targeted heating) |
Significant (oversized heaters, longer cycles) |
Long-Term Savings |
High (lower bills, fewer maintenance costs) |
Low (energy waste, frequent repairs) |
2. Reduction in Manufacturing Defects
Servo heat staking achieves defect reduction through its ability to execute precise control mechanisms with real-time modifications. Each weld produced through automated programming becomes an exact duplicate because the system operates without human intervention.
Expected temperatures are specified so that materials do not allow materials to melt or deform. Bonding uniformity is realized by maintaining constant pressure. The change to servo heat staking methods for constructing automotive door panels has resulted in manufacturers detecting 40% fewer defects.
3. Faster Production Times
Thanks to servo heat staked, production processes become faster because of their automatic control systems. Servo-driven machines operate with better performance than traditional pneumatic and manual methods.
Servo heat staking programs durable movements at high speeds that achieve shorter waiting times between production steps. The system operates with fewer mistakes because its controlled processes deliver uniform results without requiring additional work.
The use of servo heat staking in automotive production helps automotive lines complete door panel assembly operations 20–30% faster. Manufacturers benefit from faster operations that enable tight deadlines as well as production scaling and reduced labor expenses with no deterioration of product quality.
4. Increased Durability of Welded Components
Welded components can gain durability through servo heat staking. It provides precisely made high-strength bonds that pass the wear and vibration, as well as environmental pressures.
With servo-driven control, the operator generates consistent heat and pressure safely during production, eliminating all of the traditional heat-staking issues: weak material spots or breaks.
The process removes defects such as poor contact from heating too much because it forms robust connections that have lasting structural consistency. Servo heat-staked components used in automotive door panels survive daily exposure to slamming along with temperature changes and road vibrations, because they remain tight and free from cracking.
5. Consistent Production Outcomes
The uniformity of production batches through Servo heat staking comes from precise temperature and pressure controls together with repeatable cycle time management. Unlike traditional methods prone to human error or mechanical drift, servo systems are explained below:
- Eliminate Variability: The programmable features enable exact parameter replication for every weld with an accuracy of microns.
- Real-Time Monitoring: By measuring deviations such as temperature drops the system performs self-correction during the middle of a procedure.
- Scalability: The manufacturing process provides identical product quality at both high and low production volumes.
Servo heat staking applications by automotive companies produce door panel assemblies with nearly zero gap tolerance that maintain compliance with manufacturing specifications. The aerospace and medical device sectors depend on these reliability systems because their necessity for consistent operation cannot be compromised.
Applications Beyond Car Door Panels
The application of servo heat staking proves exceptional in installing car door panels but reaches many manufacturing sectors with its adaptable capabilities. Manufacturers across various industries are experiencing a revolutionary change because this technology successfully works with different materials along with intricate designs.
Key expanding applications include:
- The automotive sector utilizes this process to bond dashboards, center consoles, and seat components in an unbroken, seamless manner.
- The application of electronic components includes guard casings for smartphone and wearable technology devices in addition to IoT platforms without compromising electronic structures.
- The technology benefits Lite aerospace components by allowing panel and interior cabin bonding to produce stronger, weight-reduced aircraft components. Medical professionals use servo heat staking to join sterile, precise medical components such as insulin pumps or surgical instruments while ensuring complete residue freedom.
- Consumer goods demand strong aesthetic joints for dishwasher panels, bicycle frames, and other sporting gear.
Performance heat staking demonstrates material compatibility with thermoplastic carbon fiber and hybrid composites; therefore, it has become essential for innovative, sustainability-focused industries requiring reliable assemblies.
This technology serves a vital purpose as design complexity increases because it is essential for microelectronics and big aerospace assembly applications. Apart from this, you can opt for BYD car door panel welding because it ensures precise alignment and strong joints, significantly reducing manufacturing defects and improving overall quality.
How it Aligns with Industry Standards and Sustainability
Industry Standards:
- IATF 16949/ISO 9001: Automobile quality standards are achieved through the combination of exacting repeatable processes.
- ISO 14001: The implementation supports energy conservation while minimizing waste, thus promoting organizational environmental management systems.
- OSHA Compliance: Integrated protection systems with overload prevention along with emergency stop functionality safeguard workers on the job site.
Sustainability Goals:
- Energy Efficiency: The energy-efficient process saves between 20 and 30 percent of traditional energy usage, thereby reducing environmental carbon emissions.
- Waste Reduction: The reduction of defects to their minimum possible level supports both waste reduction and the elimination of product reprocessing.
- Chemical-Free: The adhesive-free system reduces the use of hazardous substances in compliance with RoHS regulations.
- Lightweighting: The technology used in the manufacturing process produces hybrid products that improve fuel efficiency in cars.
The Bottom Line
In conclusion, servo heat staking stands out as a reliable and efficient solution for manufacturing high-quality automotive door panels. Its precision, cost-saving benefits, and ability to work with diverse materials make it an invaluable heat staking tool for meeting the rigorous demands of the automotive industry.
By choosing our servo heat staking equipment, manufacturers can ensure superior performance and durability in their products.
Check out how our Servo Heat Staking Machine can improve your car door panel production. Visit dizo-global.com to learn about its features and why many industries choose it from trusted heat staking machine manufacturers. Contact us today for more info or to request a quote; start boosting your precision and efficiency now!
FAQs
What is servo heat staking?
Servo heat staking is a manufacturing process that uses precise heat and pressure to join components, ensuring durability and accuracy.
Why is servo heat staking suitable for automotive door panels?
It provides high precision and consistency, ensuring that door panels meet stringent quality standards.
Does servo heat staking increase production efficiency?
Yes, it streamlines the process, reduces waste, and minimizes errors, boosting overall productivity.
How does this method improve product quality?
Servo heat staking ensures strong, reliable joints and a polished finish, enhancing the durability and aesthetics of door panels.