Benefits and Applications of Ultrasonic Welder Rollers
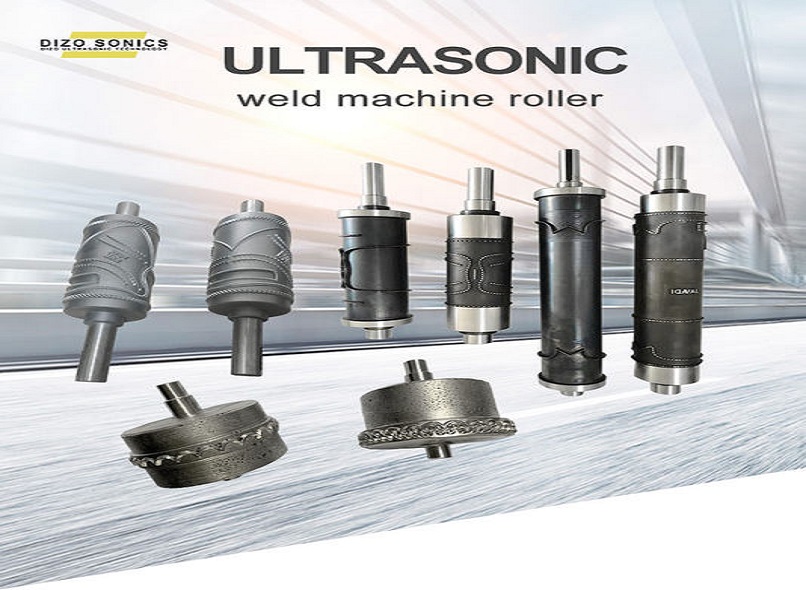
Ultrasonic welder rollers are highly efficient machines that offer numerous benefits in various industries. With their ability to provide seamless welding, cutting, and embossing, these rollers have become an essential tool in textile manufacturing, packaging, and many other applications. In this article, we will explore the advantages and applications of ultrasonic welder rollers, shedding light on their versatility and eco-friendly attributes.
What are Ultrasonic Welder Rollers?
Ultrasonic welder rollers utilize advanced technology to create continuous weld seams in a variety of materials. Unlike traditional sewing machines, these rollers operate without the need for threads, ensuring clean and precise edge banding. The key component of the ultrasonic welder roller is the rotating disc-shaped sonotrode, which generates ultrasonic vibrations to weld the materials together. This technology guarantees high stability, precise control, and excellent results in various welding applications.
Advantages of Ultrasonic Welder Rollers
Ultrasonic welder rollers offer several advantages over conventional sewing machines and other welding processes. Let's explore some of the key benefits:
- High Precision: Ultrasonic welder rollers ensure the synchronization of the welding and pressing wheels, resulting in precise and even welding without stretching, twisting, or deforming the fabric. This high level of precision is crucial in maintaining the integrity and quality of the final product.
- Waterproof and Lightweight: By eliminating the need for threads, ultrasonic welding provides a seamless and watertight bond between materials. This feature is particularly beneficial in applications where waterproofing is required, such as the production of surgical gowns, raincoats, and disposable operating coats.
- Energy Efficiency: Ultrasonic welding consumes significantly less energy compared to other thermal processes. The energy is only supplied during the welding time, reducing overall energy consumption and making it an eco-friendly choice.
- Low Maintenance: Ultrasonic tools used in welder rollers are self-cleaning, minimizing the need for frequent maintenance and cleaning. The absence of thread residues and other contaminants ensures the longevity and efficiency of the ultrasonic system.
- Versatile Applications: Ultrasonic welder rollers can be used in various industries and applications. They are suitable for welding and cutting both elastic and non-elastic textiles, allowing for the production of a wide range of products such as surgical cloths, filters, handkerchiefs, curtains, and even corsetry.
Applications of Ultrasonic Welder Rollers
Ultrasonic welder rollers find extensive use in multiple industries due to their versatility and efficiency. Here are some notable applications:
Textile Industry
In the textile industry, ultrasonic welder rollers have revolutionized the production process. They have replaced traditional sewing machines for fabric joining, enabling seamless and precise welding. Fabrics made of thermoplastic synthetic fibers can be effectively welded together, ensuring durability and maintaining the elasticity of the material. The absence of threads also eliminates the risk of fraying and enhances the overall aesthetic appeal of the finished product.
Packaging Industry
The packaging industry has also embraced the benefits of ultrasonic welder rollers. These rollers are utilized for sealing and cutting applications, ensuring the integrity and security of various packaging materials. By providing a strong and reliable bond, ultrasonic welding helps prevent leakage, contamination, and tampering in products such as food packaging, medical supplies, and consumer goods.
Automotive Industry
Ultrasonic welder rollers play a crucial role in the automotive industry. They are extensively used in the production of bellows filters for air and gasoline filtration. The precise and efficient welding provided by these rollers ensures the durability and reliability of the filters, contributing to the overall performance and longevity of vehicles.
Other Applications
Besides textiles, packaging, and automotive industries, ultrasonic welder rollers have found applications in various other sectors. Some notable examples include:
- Mesh fabric production for industrial and commercial purposes
- Manufacturing of surgical gowns and cloths for medical applications
- Creation of decorative and functional lace clothing and ribbons
- Production of air filters for agricultural machinery
- Making of various accessories such as gloves, hats, and handbags
Conclusion
Ultrasonic welder rollers offer numerous benefits and find extensive applications across various industries. With their ability to provide seamless welding, cutting, and embossing, these rollers have become an integral part of the manufacturing process. Their precision, energy efficiency, and versatility make them a preferred choice for textile, packaging, and automotive industries, among others. By embracing ultrasonic welder rollers, businesses can enhance productivity, improve product quality, and contribute to a more sustainable and eco-friendly manufacturing process.