Automotive Plastic Welding Technologies and Solutions
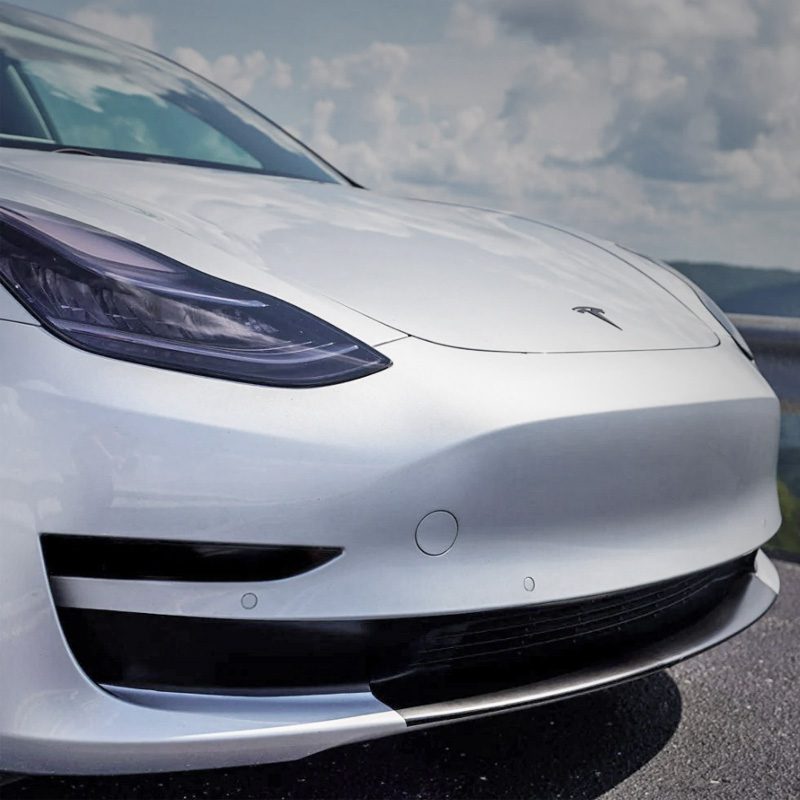
Automotive plastic welding plays a vital role in modern vehicle manufacturing and repair. As the automotive industry shifts toward lightweight, cost-effective plastic components, automotive plastic welding ensures auto parts are securely joined.
This technology offers durability, reliability, and design flexibility while reducing vehicle weight, enhancing fuel efficiency, and promoting sustainability. Automotive plastic welding also enables cost-effective repairs, reducing the need for part replacements.
With its ability to withstand stresses like vibrations and temperature changes, automotive plastic welding has become essential for ensuring the performance and longevity of vehicle components in an eco-friendly and economically viable way.
Table of Contents
Types of Plastic Welding Technologies in Automotive
Plastic Welding Solutions for Automotive Exteriors
Plastic Welding Solutions for Automotive Interiors
Benefits of Plastic Welding in the Auto Parts Industry
Key Factors for Successful Automotive Plastic Welding Projects
Choose the Right Plastic Welding Solution for Automotive Needs
Automotive Plastic Welding Equipment for Your Application
The Process of Welding Plastic Auto Parts
FAQs
Conclusion
Types of Plastic Welding Technologies in Automotive
There are five welding technologies commonly used for joining plastic parts, namely, ultrasonic welding, hot plate welding, vibration welding, laser welding, and spin welding, each with unique advantages and limitations as shown below.
Understanding these technologies helps manufacturers select the most suitable method for their needs.
1. Ultrasonic Welding: Pros and Cons
Ultrasonic welding uses high-frequency sound waves to generate heat, which melts the plastic and bonds the parts together.
Pros:
- Fast and Precise: Quick processing time and minimal post-welding cleaning.
- No Additional Materials Needed: No adhesives or fasteners required.
Cons:
- Limited to Thermoplastics: Effective mainly with thermoplastics.
- Size Constraints: Better suited for smaller parts.
2. Hot Plate Welding: Pros and Cons
Hot plate welding involves heating the surfaces of two plastic parts on a hot plate until they melt, and then pressing them together to form a bond.
Pros:
- Strong Joints for Large Parts: Ideal for thick and large components.
- Versatile: Works with a wide range of thermoplastics.
Cons:
- Slower Process: Takes longer than ultrasonic welding.
- Heat Distribution Issues: Uneven heat can lead to defects.
3. Vibration Welding: Pros and Cons
Vibration welding generates heat through the mechanical friction of one part vibrating against another, fusing the plastics. This method is ideal for large, complex parts, such as plastic welding car bumpers.
Pros:
- Strong Welds: Provides durable joints.
- No Additional Materials Needed: Similar to ultrasonic welding.
Cons:
- Noise: Generates noise and vibration.
- Heat Distribution Challenges: Can cause inconsistent melting.
4. Laser Welding: Pros and Cons
Laser welding uses a focused laser beam to melt and bond plastic materials together, offering high precision for ultrasonic welding thermoplastics and other applications.
Pros:
- Precision: Laser welding is highly precise, making it ideal for applications where tight tolerances are required.
- Clean Process: The process is clean, with minimal material waste and no need for adhesives.
- No Contact: The laser beam doesn't touch the material, reducing the risk of contamination or mechanical stress.
Cons:
- High Equipment Cost: Laser welding equipment is expensive, which may be a barrier for small manufacturers.
- Limited to Thin Materials: Laser welding is effective mainly with thin, clear plastic materials.
5. Spin Welding: Pros and Cons
Spin welding involves rotating one plastic part at high speed against a stationary part to generate heat through friction, which melts and fuses the materials.
Pros:
- Simple Process: Spin welding is easy to set up and operate, making it cost-effective for certain automotive applications.
- Strong Joints: It create strong, reliable joints suitable for auto plastic welding machines used in fuel systems or engine components.
- Minimal Setup Time: The process requires minimal setup time and integrates easily into automated production lines.
Cons:
- Limited to Circular Parts: Spin welding is most suitable for circular or cylindrical parts, limiting its versatility for more complex shapes.
- Cycle Time: The cycle time can be longer compared to methods like ultrasonic welding.
- Precision Required: Parts need to be precisely aligned, requiring additional quality control steps.
Plastic Welding Solutions for Automotive Exteriors
Automotive exteriors are a critical component of vehicle design, performance, and safety. Many of these parts, including tail lights, light strips, illuminated logos, and bumpers, are made from durable plastic materials that require specialized welding solutions for effective assembly.
Plastic welding ensures that these exterior parts are securely joined, capable of withstanding various environmental factors, and capable of performing under the stresses of daily use. Below, we explore how plastic welding technologies are applied to automotive exteriors and their specific benefits for key components.
1. Tail Lights
One of the most common uses of automotive plastic welding in exterior components is in the production of tail lights. These parts are made from materials like polycarbonate and PMMA, offering clarity and impact resistance. Plastic welding is critical in joining the light housing with lenses, ensuring the final product is both strong and airtight.
2. Light Strips
LED light strips are increasingly popular in automotive design, used as accent lighting along grilles, side panels, or rear lights. These strips require clean, precise welds to secure them without damaging delicate electronics.
3. Illuminated Logos
Illuminated logos are becoming a common feature in modern automotive design, enhancing the vehicle's look. These logos often incorporate LED lighting, and plastic welding ensures they are securely attached without damaging their electrical components or aesthetics.
4. Car Bumpers
Plastic welding is essential in assembling automotive bumpers, designed to absorb impacts and protect the vehicle's bodywork. Automotive plastic welding techniques help ensure these components are securely joined, maintaining strength and durability over time. The use of plastic welding machines for car bumpers is key to producing high-quality, impact-resistant joints.
Plastic Welding Solutions for Automotive Interiors
Automotive interior components, such as dashboards, center panels, and seating parts, rely heavily on automotive plastic welding technologies for secure, durable, and precise assembly.
Dashboard Assembly
The dashboard requires robust welding to secure components like air vents and control panels. Ultrasonic welding is often used for small, intricate parts, providing clean, strong bonds without damaging sensitive elements.
Center Panel and Console
The center panel houses key vehicle controls. Vibration welding and ultrasonic welding are used to join large and small plastic components, ensuring both structural integrity and ease of use. These technologies are critical in applications such as plastic welding car bumpers and auto body panels.
Instrument Cluster and Dashboard Inserts
Plastic welding techniques, such as spin welding and laser welding, ensure that instrument clusters are securely assembled without compromising visual clarity or functionality. These technologies are crucial for precise alignment and durability.
Glove Box
The glove box assembly uses hot plate welding for larger parts, while ultrasonic welding is employed for intricate areas, such as securing locking mechanisms. These methods ensure a tight, durable bond while preserving the interior aesthetics.
Seating Components
Seating parts, including seat bases and armrests, rely on vibration welding to connect plastic to metal frames, ensuring long-lasting performance. Ultrasonic welding is also used for smaller components like seat belt anchors and adjustment mechanisms.
Benefits of Plastic Welding in the Auto Parts Industry
Plastic welding is essential in automotive manufacturing due to its numerous benefits:
- Strong and durable bonds: Essential for parts like car bumper plastic welding and auto body panel welding.
- Versatility: It works with various plastics (ABS, polypropylene, etc.) and is suitable for both simple and complex parts like instrument clusters and fuel tanks, ensuring reliable joins across diverse materials.
- Cost-Effectiveness: Plastic welding machines offer reduced material costs by eliminating the need for adhesives or mechanical fasteners.
- Consistent Results: Plastic welding ensures uniform, high-quality joins, which is essential for meeting the strict tolerance and safety standards required in the automotive industry.
- No Surface Damage: With processes like ultrasonic welding, the parts' surfaces remain unscathed, preserving the aesthetic quality of sensitive components such as interior panels.
- Environmentally FriendlyBenefits: By reducing the use of adhesives and chemicals, plastic welding minimizes waste and supports the recycling of plastics, making it a sustainable manufacturing choice.
Key Factors for Successful Automotive Plastic Welding Projects
Successful automotive plastic welding depends on several critical factors, all of which ensure that the process is efficient, precise, and durable. The plastic welding machine for car bumper should be chosen based on material compatibility and weld strength for the best results.
Material Compatibility
It's crucial to select compatible materials for welding, such as ABS or polypropylene, as each plastic type has its own melting point, which can affect the quality of the weld. Using the right combination ensures strong and long-lasting bonds.
Thorough Surface Preparation
Cleaning the surfaces to be welded is essential. Any contaminants such as dirt, oil, or moisture can interfere with the welding process and lead to weak or faulty joints.
Skilled Operators
Skilled operators are key to achieving consistent and high-quality welds. Experience and knowledge of welding parameters ensure that the process runs smoothly and that the desired bond strength is achieved.
Plastic Welding Machine Type
The choice of welding machine—whether it's ultrasonic, vibration, or hot plate welding—depends on the materials being used and the desired result. Each machine has its own set of advantages for different applications.
Plastic Welding Parameters
Parameters such as temperature, pressure, and vibration frequency must be accurately controlled to achieve optimal results. Small deviations can lead to inconsistent joints or material degradation.
Precision and Control
Precision is critical in automotive plastic welding, particularly for high-stress parts. Advanced machines offer automated control to ensure tight tolerances and minimize human error.
Welding Tools and Fixtures
Properly designed tools and fixtures help hold the parts in place during welding. The right setup minimizes the chances of misalignment, ensuring consistent, high-quality welds.
Plastic Welding Speed
The speed of the welding process should be optimized to balance productivity with quality. Too fast a process may reduce the strength of the joint, while slow welding can be inefficient for high-volume production.
Welding Machine Maintenance and Calibration
Regular maintenance and calibration of the welding machines ensure that they function correctly and produce reliable results.
Power Supply and Stability
A stable power supply is essential to ensure that welding equipment operates at the required power levels. Fluctuating power can result in inconsistent welds.
Environmental Factors
Factors such as temperature and humidity can affect the welding process, especially in outdoor or unregulated environments. Ensuring controlled conditions can prevent potential issues.
Choose the Right Plastic Welding Solution for Automotive Needs
When selecting the best plastic welding solution for automotive applications, several factors should be considered:
- Cost: Evaluate both initial equipment costs and ongoing operational expenses. Technologies like ultrasonic welding or vibration welding vary in price, so finding the most cost-effective option is key for high-volume production.
- Durability: The weld must endure harsh conditions. Ensure the chosen welding method provides strong, lasting bonds, especially for materials like ABS or polypropylene.
- Material Compatibility: Different welding methods work best with specific plastics. Understanding the material's properties and selecting the right technique ensures effective bonding.
- Expert Recommendations: Consult industry professionals for advice on the best welding solution for your needs. Experts can guide you in choosing the right technology for different automotive components.
- Top Brands and Suppliers: Opt for reliable plastic welding machine manufacturers or local suppliers who provide quality equipment and support. Trusted brands ensure better performance and fewer maintenance issues.
Plastic welding machine manufacturers provide valuable insights into choosing the right welding technique based on material types such as polypropylene and ABS. It is proper to consult experts on ultrasonic welding materials for specific components like car bumpers and car body panels.
Automotive Plastic Welding Equipment for Your Application
How Does a Plastic Welding Machine Work?
A plastic welding machine uses heat, pressure, or ultrasonic energy to melt and bond plastic parts together. Depending on the welding technique—such as ultrasonic, vibration, or hot plate welding—it applies controlled energy to create a strong, durable joint.
Plastic Welding Machines in Other Industries
Plastic welding machines are also used in industries beyond automotive:
- Aerospace: For precise, high-strength bonding in lightweight aircraft components.
- Medical: To assemble medical devices like syringes and tubing without leaks.
- Home Appliances: In the production of strong, durable seals for appliances like refrigerators and washing machines.
Your Trusted Plastic Welding Machine Manufacturer
Partnering with a trusted manufacturer like Dizo Global ensures top-quality, custom plastic welding machines designed for automotive needs.
Dizo Custom Plastic Welding Machines for Automotive Parts
Dizo offers specialized welding machines for automotive needs:
- Car Bumper Ultrasonic Welder: Precise welding for durable bumpers, ensuring strong and clean joints without damage to the surrounding material.
- Car Door Panel Heat Staking Machine: High-strength bonding for door panels, providing a robust and long-lasting connection that withstands the test of time and impact.
- Auto Interior Parts Ultrasonic Welder: Efficient welding for interior components, offering quick and reliable results with minimal thermal impact on sensitive parts.
- Car Interior Components Plastic Welder Workstation: For welding parts like center consoles and glove boxes, enabling flexible and ergonomic production of complex interior components.
- Heat Staking & Hot Plate Welding Machine: For larger, high-temperature automotive parts, delivering strong, precise welds on large components while maintaining structural integrity.
- Car Exterior Parts Multi-Head Ultrasonic Welder: For welding multiple exterior components simultaneously, improving production efficiency by reducing cycle times while ensuring precise welds.
With Dizo, manufacturers get the right equipment to enhance production quality and efficiency in automotive plastic welding.
The Process of Welding Plastic Auto Parts
Welding plastic auto parts involves several essential steps to ensure strong, durable bonds:
1. Prepare the Surfaces
Before starting automotive plastic welding, it's important to clean the parts thoroughly to remove dirt, grease, and other contaminants. This ensures proper adhesion during the welding process.
2. Choose the Welding Method
The method chosen depends on the plastic material and part design. Common techniques include ultrasonic welding, hot plate welding, and vibration welding. For example, ultrasonic welding thermoplastics is ideal for small parts like car center consoles, while hot plate welding works well for larger parts like plastic welding car bumpers.
3. Set Up the Equipment
The auto plastic welding machine should be calibrated correctly for temperature, pressure, and speed. Proper setup of the equipment ensures that the right settings are in place to create strong welds.
4. Heat the Plastic
The plastic parts are heated to a temperature that makes them malleable but not molten. This step is crucial to avoid overheating, especially when welding parts like plastic welding car bumpers.
5. Apply Pressure
Once the plastic is heated, pressure is applied to fuse the parts together. This creates a strong bond, and is a vital step for ensuring that the weld is secure.
6. Cool the Plastic
After welding, it's important to allow the parts to cool and solidify. Proper cooling ensures that the weld remains strong and durable.
7. Finish the Welded Part
After cooling, excess material is trimmed, and the weld is inspected to ensure it meets quality standards. This final step guarantees that the part is ready for use and functions as expected.
By following these steps, automotive plastic welding ensures strong, durable connections in plastic auto parts, improving the performance and longevity of the vehicle.
FAQs
1. Are plastic welds strong?
Yes, plastic welds can be very strong, often as strong as or stronger than the original material. The key to strong welds lies in choosing the right welding method, such as using a high-quality auto plastic welding machine.
2. Can you weld on modern cars?
Modern vehicles use a variety of plastics in components like bumpers, dashboards, and interior panels. Plastic welding techniques like ultrasonic welding and vibration welding are ideal for these applications, ensuring durable repairs for parts like car center consoles and plastic welding car bumpers.
3. What industries use plastic welding?
Plastic welding is used in multiple industries, including:
- Automotive: For parts like bumpers and dashboards.
- Aerospace: For lightweight, durable parts.
- Medical: For creating sterile, precision devices.
In the automotive sector, automotive plastic welding is essential for manufacturing and repairing plastic parts, from bumpers to interior components.
4. How is welding used in the automotive industry?
In automotive applications, welding is used to assemble, repair, and manufacture parts like plastic welding car bumpers and auto plastic welding kits. This process enhances the durability and functionality of automotive parts, ensuring long-lasting, reliable connections.
5. What are the disadvantages of plastic welding?
Some challenges include:
- Material Compatibility: Not all plastics are weldable.
- Skill Required: Expertise is necessary for effective welding.
- Limited to Thermoplastics: Plastic welding only works on thermoplastics, limiting its use in some automotive applications.
Conclusion
In conclusion, automotive plastic welding is essential for the modern automotive industry, offering solutions that improve the durability, efficiency, and sustainability of vehicle manufacturing.
Technologies like vibration welding, ultrasonic welding, and hot plate welding allow manufacturers to join plastic parts with precision and strength, resulting in cost-effective and environmentally friendly solutions.
Future innovations in plastic welding technologies will drive stronger, more sustainable solutions. Ultimately, staying ahead of these advancements is key for manufacturers to remain competitive and meet the evolving needs of the automotive market.