ABS Plastic Welding Guide: Methods, Tools & Tips
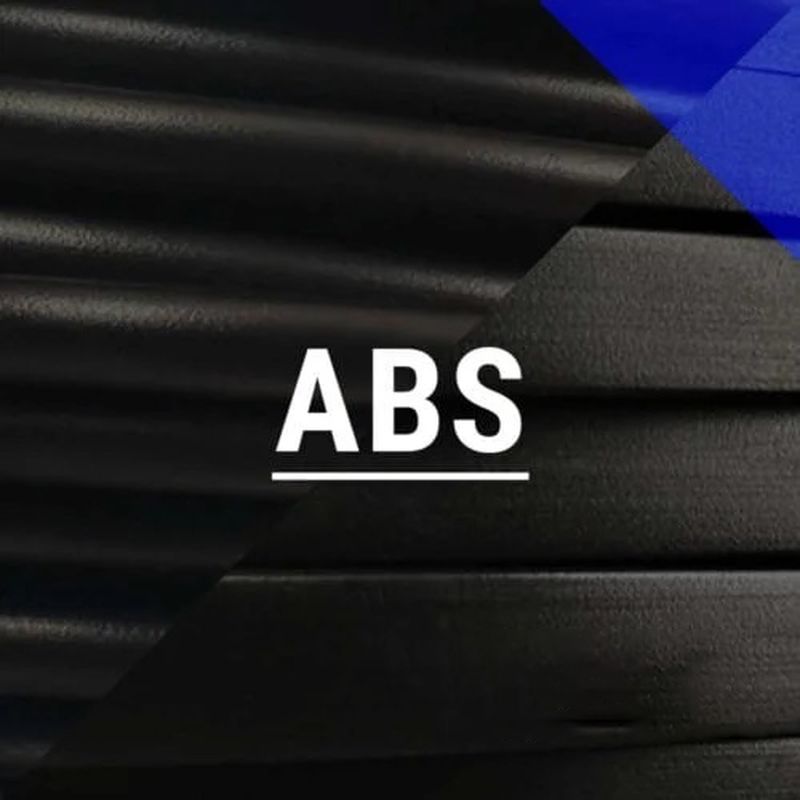
ABS (acrylonitrile butadiene styrene) is a high-impact thermoplastic widely used in automotive bumpers, consumer electronics, and industrial components.
Its molecular structure—a copolymer of acrylonitrile, butadiene, and styrene—provides exceptional impact resistance and thermal stability, with a glass transition temperature of 105°C (221°F) per ASTM D3965. Compared to PVC, ABS offers 20% higher impact resistance, making it ideal for structural welding.
Key Performance Data:
- Welded joints achieve 95% of base material strength under AWS G1.10M standards.
- Automotive manufacturers like Toyota and Honda use ABS ultrasonic welding for dashboard assemblies, which reduces assembly time by 65% while maintaining ISO 9001 compliance Toyota Technical Report.
Table of Contents
Why Weld ABS Plastic?
Methods of ABS Welding
Choosing the Right ABS Welding Method
ABS Welding Preparation Checklist
Plastic Welding Tools and Equipment for ABS Welding
Common Mistakes to Avoid in ABS Plastic Welding
Troubleshooting Common Issues in ABS Plastic Welding
Why Weld ABS Plastic?
Key Benefits of ABS Welding
Superior Bond Strength: Laboratory tests by Smithers show welded ABS joints exhibit 300% more strength than adhesive bonds, with ultrasonic welds achieving 90% of the original material strength.
Practical Durability:
- BMW uses vibration welding for bumper components to meet crash safety standards (BMW Group Innovation).
- Siemens Healthineers employs laser welding for medical-grade ABS housings, ensuring sterility and dimensional accuracy.
Consistent Quality: Modern ultrasonic welding systems deliver weld strengths within ±5% variation (per ISO 9001:2005 standards), ensuring reliable production outcomes.
Versatile Applications: Acrylonitrile butadiene styrene plastic can be welded using methods like:
- Hot plate welding (ideal for large automotive panels)
- ABS ultrasonic welding (precision electronics and medical devices)
- Laser welding (used in medical-grade components)
Case Study: A leading automotive supplier has achieved a 40% reduction in joint failures after switching from adhesive bonding to ultrasonic welding for ABS dashboard assemblies. The improved process also reduced assembly time by 65% while maintaining consistent joint quality across 100,000+ units annually.
Methods of ABS Welding
ABS plastic welding techniques vary based on part geometry, strength requirements, and production scale. Below is a detailed comparison:
Comparative Analysis of Techniques
Method |
Best For |
Key Parameter |
Equipment |
---|---|---|---|
Hot Plate Welding |
Large automotive panels |
270–310°C (518–590°F) plate temperature |
Dizo NC-F Series |
Ultrasonic Welding |
Medical devices (e.g., insulin pumps) |
0.5–2.0 MPa hold pressure |
Dizo DZ-200 |
Spin Welding |
Cylindrical parts (fuel filters) |
1000–3000 RPM rotation speed |
Dukane IQ Series |
Choosing the Right ABS Welding Method
Below are key factors when selecting the optimal ABS welding technique:
Figure 1: ABS Welding Method Selection Criteria
1. Part Geometry
- Large, flat surfaces (>100mm²): Hot plate welding or vibration welding provides uniform heat distribution
- Cylindrical parts: Spin welding ensures consistent circumferential bonds
- Intricate designs: ABS ultrasonic welding or solvent welding offers precise control
2. Strength Requirements
Select the plastic welding method based on strength requirements:
- Structural components: Hot plate welding or ultrasonic welding (95% base strength).
- Non-critical assemblies: Solvent welding.
3. Equipment Accessibility
- Industrial setting: Access to specialized equipment enables ultrasonic welding or hot plate welding
- Limited resources: Solvent welding requires minimal equipment investment
4. Production Scale
- High-volume: Automated ultrasonic systems .
- Low-volume: Hot plate welders (e.g., Dizo NC-F Series).
Solvent Welding Guide for ABS Plastic
Step 1: Safety First
- Required PPE: Chemical-resistant nitrile gloves, safety goggles, and respirator mask rated for organic vapors
- Work in a well-ventilated area or use local exhaust ventilation
Step 2: Material Selection
- Solvent options: MEK (recommended) or acetone
- Note: MEK provides stronger bonds but requires strict safety precautions
Step 3: Surface Preparation
- Clean surfaces thoroughly with isopropyl alcohol
- Sand if needed, using 220-grit sandpaper
- Remove all dust with compressed air or lint-free cloth
Step 4: Solvent Application
- Use the precise applicator brush
- Apply a thin, even layer to both surfaces
- Work quickly - solvent evaporates in 30-60 seconds
Step 5: Joint Assembly
- Align parts immediately after solvent application
- Apply firm, even pressure (2-5 psi recommended)
- Hold for 60 seconds minimum
Step 6: Curing Schedule
- Initial set time: 2-4 hours
- Handling strength: 24 hours
- Full cure strength: 48-72 hours at room temperature
Important: Temperature and humidity affect curing times. For critical applications, extend cure time by 50% if humidity exceeds 80% or the temperature is below 20°C (68°F).
Ultrasonic Welding Guide for ABS Plastic
Step 1: Equipment Setup and Safety
- Required PPE: Safety glasses, hearing protection
- Verify welder calibration (20-40 kHz range)
- Check horn condition and mounting
Step 2: Part Positioning
- Clean fixture surfaces
- Align parts within ±0.1mm
- Verify energy director geometry if applicable
Step 3: Welding Parameters
- Initial settings: 20 kHz frequency, 60% amplitude
- Weld time: 0.2-0.5 seconds typical
- Hold pressure: 0.5-2.0 MPa
Step 4: Process Monitoring
- Monitor power curve during welding
- Verify collapse distance meets the specification
- Allow cooling under pressure (3-5 seconds)
Step 5: Quality Verification
- Visual inspection for flash and sink marks
- Check weld strength (destructive testing on samples)
- Document parameter settings for successful welds
Hot Plate Welding Process for ABS Plastic: Step-by-Step
- Surface Preparation: Thoroughly clean ABS surfaces and remove contaminants. Light sanding may be required for optimal surface contact.
- Temperature Control: Set hot plate temperature between 270°C-310°C (518°F-590°F). Begin at a lower range to prevent material degradation.
- Surface Melting: Apply controlled pressure to press components against hot plate until achieving uniform melt pattern.
- Joint Formation: Remove parts from heat source and immediately join with specified pressure (typically 0.5-2.0 MPa).
- Quality Inspection: After cooling, examine the weld quality for complete fusion, proper alignment, and structural integrity.
Critical Temperature Control: Maintaining precise temperature (270°C-310°C) is essential for optimal molecular bonding. Insufficient heat prevents proper fusion, while excessive temperature risks material degradation.
ABS Welding Preparation Checklist
Step 1: Surface Cleaning
- Use isopropyl alcohol to remove oils (avoid paper towels).
- Sand with 120–220 grit sandpaper for enhanced adhesion.
Step 2: Material Verification
- Confirm acrylonitrile butadiene styrene plastic via recycling code "7" or "ABS" markings.
Step 3: Equipment Calibration
- Validate ABS plastic welding temperature (270–310°C) using calibrated tools.
Plastic Welding Tools and Equipment for ABS Welding
Essential Tools for ABS Welding: Complete Guide for Beginners & Pros
Below is a comprehensive breakdown of the required tools for each ABS welding technique, including OSHA-compliant safety equipment and recommended budget options.
Hot Plate Welding Equipment
Hot Plate Welder
- Budget Option: Dizo NC-E - Ideal for beginners
- Professional Choice: NC-F - Industrial-grade precision
- Required Specs: Adjustable temperature control (270°C-310°C)
Support Equipment
- Industrial-grade clamps ($30-50/pair)
- Infrared thermometer with laser targeting ($25-40)
Solvent Welding Kit
Essential Tools
- PTFE-tipped applicator brush set ($12-15)
- MEK solvent (OSHA-approved container, $20/500ml)
- Chemical-resistant cleaning cloths ($8/pack)
Ultrasonic Welding Station
Professional Equipment
- Entry-level: Dizo DZ-200
- Production: Dukane IQ Series ($5,000+)
- Precision-machined fixtures ($200-500/set)
OSHA-Compliant Safety Equipment
Per OSHA Standard 1910.94(d)(2), adequate ventilation must provide minimum 100 feet/minute air velocity across the welding area:
Personal Protection
- Chemical-resistant nitrile gloves (ANSI/ISEA 105-2016 rated)
- 1-certified safety goggles
- NIOSH-approved respirator (OV/AG/P100 filters)
Ventilation Requirements
- Local exhaust system (minimum 100 CFM)
- Fume extraction hood for enclosed spaces
Beginner vs. Pro Tool Comparison
Tool Category |
Beginner Kit ($300-500) |
Professional Setup ($3000+) |
---|---|---|
Welding Equipment |
Basic hot plate welder |
Ultrasonic + hot plate systems |
Safety Gear |
Basic PPE kit |
Full respiratory system |
Accessories |
Manual clamps |
Pneumatic fixtures |
Optional Enhancement Tools
Surface Preparation
- Professional sanding kit (120-220 grit)
- Digital surface roughness tester
Supplementary Equipment
- Digital heat gun with LCD ($45-60)
- ABS welding rods (ISO 9001 certified)
Common Mistakes to Avoid in ABS Plastic Welding
Critical Tips for Strong ABS Welds: Avoid These Common Mistakes
Getting perfect ABS welds requires attention to detail and proper technique. Let's explore the most critical mistakes and their solutions, backed by expert insights:
Essential Safety and Preparation
Surface Preparation
- Mistake: Dirty or contaminated surfaces
- Solution: Clean thoroughly with an appropriate solvent, remove oxidation layer
- Best Practice: Visual inspection should show a matte, uniform surface
Temperature Control
- Mistake: Operating outside 270-310°C range
- Solution: Use calibrated equipment, monitor temperature
- Warning: Incorrect temperature leads to weak bonds or material degradation
Technical Considerations
Filler Material Selection
- Mistake: Incompatible filler rod material
- Solution: Match filler rod to base ABS type
- Pro Tip: Check manufacturer specifications for compatibility
Pressure Application
- Mistake: Inconsistent or improper pressure
- Solution: Maintain steady pressure (recommended: 0.5-2.0 MPa)
- Quality Check: Look for uniform melt pattern
Process Excellence
Technique Mastery
- Mistake: Poor welding technique or insufficient practice
- Solution: Practice on scrap material first
- Success Indicator: Consistent, smooth weld appearance
Quality Control
- Mistake: Skipping inspection steps
- Solution: Implement a systematic weld inspection protocol
- Key Checks: Look for cracks, voids, or discoloration
Remember: Proper PPE (safety goggles, heat-resistant gloves) and adequate ventilation are non-negotiable safety requirements for all ABS welding operations.
Troubleshooting Common Issues in ABS Plastic Welding
Understanding and resolving ABS welding issues requires systematic analysis and proper corrective actions. Below is a comprehensive troubleshooting guide based on Dizo industrial welding standards and expert analysis.
Issue |
Common Causes |
Solution |
---|---|---|
Incomplete Fusion |
Low temperature, insufficient pressure, contaminated surfaces |
Increase temperature to 270-310°C, verify pressure (0.5-2.0 MPa), and clean with approved solvent |
Warping |
Uneven heating, inadequate fixturing |
Use a proper jigging system, implement balanced heat distribution |
Poor Weld Strength |
Improper parameters, material mismatch |
Verify material compatibility, adjust parameters per manufacturer specs |
Surface Cracking |
Rapid cooling, excessive heat |
Control cooling rate, maintain optimal temperature range |
Advanced Failure Analysis Techniques
Non-Destructive Testing (NDT)
- Dye penetrant testing for micro-cracks (per ASTM E1417).
- Ultrasonic inspection for internal voids (MISTRAS Group).
Quality Control Measures
Process Verification
- Temperature mapping using infrared thermography
- Pressure distribution analysis with sensitive films
- Weld zone microscopic examination
For consistent, high-quality ABS welds, follow these key steps:
1. Pre-Weld Checklist
- Verify material compatibility and cleanliness
- Calibrate equipment parameters
- Document environmental conditions
2. During Welding
- Monitor temperature and pressure continuously
- Maintain proper alignment and fixturing
- Record process parameters for traceability
3. Post-Weld Inspection
- Perform visual and NDT inspections
- Document results and any anomalies
- Validate mechanical properties if required