Vibration Welding Manufacturing
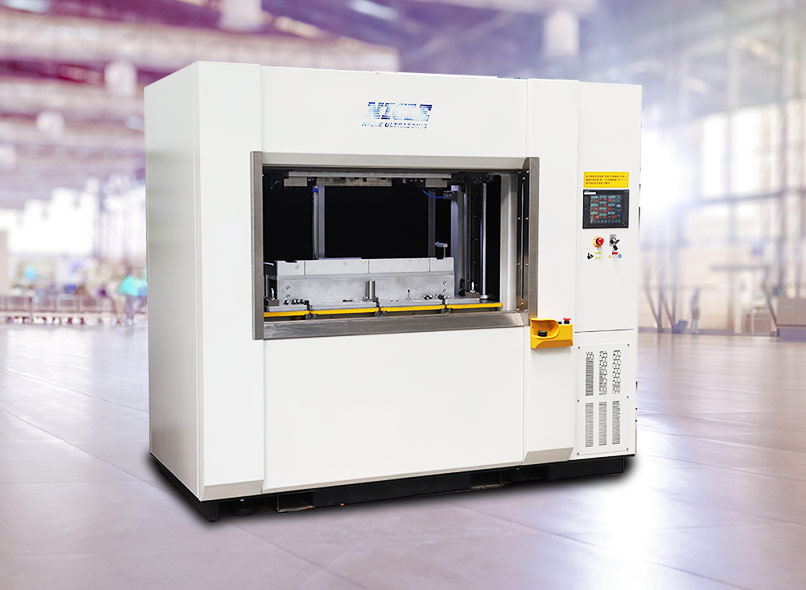
Vibration welding manufacturing is a frictional welding technique that offers numerous advantages for joining thermoplastic parts. By utilizing the principles of vibration and friction, this process creates strong, airtight welds that are ideal for a wide range of applications. In this comprehensive guide, we will explore the process of vibration welding manufacturing, its advantages and disadvantages, as well as its various applications in different industries.
Why Choose Vibration Welding Manufacturing?
Vibration welding manufacturing is a cost-effective and efficient method for bonding thermoplastic components. Unlike other welding techniques that require additional materials or heat sources, vibration welding relies on the friction generated by vibrating the parts together under pressure. This eliminates the need for consumables, reduces cycle times, and produces high-strength, hermetic welds. Additionally, vibration welding is compatible with most thermoplastics and can join dissimilar materials.
Who Can Benefit from Vibration Welding Manufacturing?
Vibration welding manufacturing is an excellent choice for design engineers and manufacturers working with thermoplastic parts. Its versatility makes it suitable for a wide range of industries, including automotive, aerospace, appliance manufacturing, and more. Whether you are looking to join large parts or complex shapes, vibration welding can provide reliable and efficient results.
Is Vibration Welding Manufacturing Right for Your Project?
Before diving into the details of vibration welding manufacturing, it's important to determine if it is the right welding technique for your specific project. While vibration welding offers many advantages, it also has some limitations. For instance, it may not be suitable for low modulus thermoplastics or joints between plastics with significantly different melting temperatures. Furthermore, the vibration involved in the process may not be suitable for sensitive or miniature components. However, if your project requires fast cycle times, strong welds, and the ability to join various thermoplastics, vibration welding manufacturing may be the perfect solution.
Advantages of Vibration Welding Manufacturing
Vibration welding manufacturing offers numerous advantages that make it a preferred choice for joining thermoplastic parts. Let's explore some of these benefits in detail:
1. Strong and Airtight Welds
One of the key advantages of vibration welding manufacturing is its ability to produce strong and airtight welds. By generating heat through friction at the joint interface, the melted plastic forms a molecular bond when cooled. This results in a weld that is as strong as the bulk material, ensuring the integrity of the joined parts.
2. Fast Cycle Times
Vibration welding manufacturing is known for its fast cycle times, making it highly efficient for mass production. The process of vibrating the parts together under pressure generates heat quickly, allowing for rapid melting and solidification of the weld. This means that parts can be joined in a matter of seconds, significantly reducing production time.
3. Compatibility with Most Thermoplastics
Another advantage of vibration welding manufacturing is its compatibility with a wide range of thermoplastics. Whether you are working with amorphous resins like ABS/PC, PVC, PMMA, or semi-crystalline materials such as HDPE, PA, PP, vibration welding can effectively join them. It can also handle materials with up to 45 percent filler content, making it a versatile option for various applications.
4. Ability to Join Dissimilar Materials
Vibration welding manufacturing is not limited to joining similar materials. It can also successfully join dissimilar materials with compatible melting points. This opens up new possibilities for combining different thermoplastics or creating composite structures, expanding the design options for engineers and manufacturers.
5. No Consumables or Emissions
Unlike some other welding techniques that require additional materials or generate fumes, vibration welding manufacturing is a clean and environmentally friendly process. It does not require any consumables such as fasteners, adhesives, or solvents. This not only reduces production costs but also makes it easier to disassemble and recycle the welded parts.
6. Multiple Parts per Cycle
Vibration welding manufacturing allows for the simultaneous welding of multiple parts in a single cycle. This makes it suitable for high-volume production, where efficiency and productivity are key considerations. By welding multiple parts at once, manufacturers can significantly increase throughput and reduce production time.
7. Easily Automated
Vibration welding manufacturing is well-suited for automation, making it ideal for high-volume production lines. The process can be integrated into automated systems, allowing for seamless and consistent welding of parts. By automating the process, manufacturers can achieve higher precision, reduce the risk of human error, and increase overall productivity.
8. Low Maintenance and Power Consumption
Vibration welding manufacturing machines require minimal maintenance, resulting in reduced downtime and increased production efficiency. Additionally, these machines are energy-efficient, consuming less power compared to other welding techniques. This not only contributes to cost savings but also aligns with sustainability goals.
9. Quick Change Tooling
Vibration welding manufacturing offers the advantage of quick change tooling. This means that manufacturers can easily switch between different parts without the need for extensive reconfiguration. Quick change tooling reduces downtime and allows for more flexibility in production, making it easier to accommodate different product variations or design changes.
These advantages make vibration welding manufacturing an attractive choice for industries looking to achieve strong, efficient, and cost-effective bonding of thermoplastic parts. Whether you are in the automotive, aerospace, or appliance manufacturing industry, vibration welding can offer significant benefits for your production processes.
Disadvantages of Vibration Welding Manufacturing
While vibration welding manufacturing offers numerous advantages, it also has some limitations and disadvantages that need to be considered. Let's explore these drawbacks in detail:
1. Unsuitable for Low Modulus Thermoplastics
Vibration welding manufacturing may not be suitable for joining low modulus thermoplastics. Low modulus materials have a lower stiffness and may not respond well to the vibration and pressure applied during the welding process. This can result in poor weld quality or even failure of the joint.
2. Not Ideal for Joints with Significant Melting Temperature Differences
Vibration welding manufacturing is less suitable for joining plastics with significantly different melting temperatures. The process relies on generating heat through friction, and if the melting temperatures of the two materials are too different, it can lead to imbalanced melting and poor weld quality.
3. Sensitivity to Sensitive or Miniature Components
The vibration involved in the welding process may not be suitable for sensitive or miniature components. The mechanical forces exerted during vibration welding can potentially damage or alter the integrity of delicate parts. In such cases, alternative welding techniques or assembly methods should be considered.
4. Flash Formation
Flash formation is a common occurrence in vibration welding manufacturing. Flash refers to the excess molten material that flows out of the joint during the welding process. While it can be trimmed or removed post-welding, it may affect the aesthetics of the finished product. Design considerations should be made to minimize flash formation or conceal it in areas that do not impact the appearance or functionality of the part.
5. Limited Joint Geometries
Vibration welding manufacturing is most suitable for joining parts with flat or relatively flat seams. Complex or curved joint geometries may pose challenges for vibration welding. In such cases, alternative welding techniques or design modifications may be required to achieve the desired joint integrity.
Despite these limitations, vibration welding manufacturing remains a highly effective and widely used technique for joining thermoplastic parts. By understanding its limitations and considering the specific requirements of your project, you can harness the benefits of vibration welding while mitigating any potential drawbacks.
Component Size Considerations in Vibration Welding Manufacturing
One important aspect to consider in vibration welding manufacturing is the size of the components being welded. While vibration welding is capable of joining large parts, there are certain considerations to keep in mind.
1. Fixture Design and Alignment
To ensure successful welding of large parts, proper fixture design and alignment are crucial. The fixtures should securely hold the parts in place and provide adequate support throughout the welding process. This helps maintain alignment and prevents any movement or misalignment during vibration welding.
2. Clamping Force
Clamping force is an important factor in vibration welding, especially when dealing with larger parts. Sufficient clamping force is necessary to ensure proper contact between the parts and promote effective heat generation through friction. The clamping force should be evenly distributed across the joint to achieve consistent weld quality.
3. Welding Time and Cooling
The size of the components will also affect the welding time and cooling process. Larger parts may require longer welding times to ensure proper melting and bonding of the joint. Similarly, cooling times may be extended to allow for complete solidification and to ensure the weld reaches its optimum strength. Proper consideration of these factors is essential to achieve reliable and high-quality welds in larger components.
Other Bonding Options
While vibration welding manufacturing is a highly effective technique for joining thermoplastic parts, it is not the only option available. Depending on the specific requirements of your project, you may consider alternative bonding methods. Let's explore some of these options:
1. Screwing Parts Together
For parts that do not require a permanent bond, screwing them together can be a viable option. This allows for easy disassembly and reassembly, making it suitable for applications that may require maintenance or component replacement.
2. Gluing Parts Together
Adhesive bonding, or gluing, is another commonly used method for joining thermoplastic parts. Adhesives provide a strong and permanent bond between the parts, allowing for a wide range of design possibilities. However, adhesive bonding may require additional curing time and may not be suitable for high-temperature or high-stress applications.
3. Ultrasonic Welding
Ultrasonic welding is another popular technique for joining thermoplastics. It utilizes high-frequency ultrasonic vibrations to create frictional heat at the joint interface, similar to vibration welding. However, ultrasonic welding operates at higher frequencies and lower amplitudes compared to vibration welding. This technique is particularly suitable for small to medium-sized parts and offers fast cycle times.
4. Infrared Welding
Infrared welding utilizes infrared radiation to heat the joint area between thermoplastic parts. The heat generated softens the material, allowing for fusion and bonding of the parts. Infrared welding is often used for larger parts or complex shapes where vibration welding may not be suitable. It offers precise control over the heating process and can achieve high-quality welds.
When considering alternative bonding options, it's important to evaluate the specific requirements of your project, including the size and geometry of the parts, desired cycle times, and the need for a permanent or reversible bond. Each bonding method has its advantages and limitations, and the choice will depend on factors such as joint strength, aesthetics, production volume, and cost considerations.
About Xfurth Ltd
Xfurth Ltd is a leading supplier and manufacturer of plastic welding and joining systems. With a focus on providing high-quality equipment and services, Xfurth offers a range of ultrasonic and spin welding equipment, along with tooling, designed and manufactured in the UK. They are committed to meeting the individual needs of their customers and offer prompt technical support and spare parts availability.
As official UK supply partners for CEMAS, a renowned manufacturer of advanced thermoplastic systems, Xfurth provides a comprehensive range of vibration welding machines. These machines are highly customizable and can be tailored to meet specific application requirements. With a strong emphasis on safety, quality, and customer satisfaction, Xfurth is a trusted partner for all your plastic assembly needs.
Choosing a Vibration Welding Machine
When selecting a vibration welding machine, several factors need to be considered to ensure the machine meets your specific requirements. Let's explore some important considerations:
1. Machine Type and Size
Vibration welding machines come in various types and sizes, ranging from manually operated machines to fully automated systems. The type and size of the machine will depend on factors such as the size and complexity of the parts being welded, production volume, and the level of automation desired.
2. Vibration Technology
Different vibration welding machines may utilize various vibration technologies. It's essential to understand the specific vibration technology employed by the machine and how it aligns with your project requirements. Whether it's linear vibration welding or orbital vibration welding, each technology has its strengths and limitations.
3. Tooling Design and Flexibility
The tooling design and flexibility of a vibration welding machine are crucial considerations. The machine should allow for quick and easy changeover of tooling to accommodate different part geometries. Flexibility in tooling design ensures proper alignment and adequate support for the parts, promoting consistent and high-quality welds.
4. Automation and Integration Capabilities
Automation and integration capabilities are important, especially for high-volume production. Consider whether the machine can be seamlessly integrated into an automated production line and whether it offers features such as programmable controllers and data logging for process optimization and quality control.
5. Maintenance and Support
Ensure that the vibration welding machine you choose comes with reliable maintenance and technical support. Regular maintenance is essential for optimal machine performance and longevity. Additionally, having access to prompt technical support and spare parts availability will minimize downtime and ensure uninterrupted production.
By carefully considering these factors and assessing your specific project requirements, you can select the right vibration welding machine that aligns with your production goals and delivers consistent, high-quality welds.
CEMAS Vibration Machines
CEMAS is a leading manufacturer of vibration welding machines, known for their innovative designs and superior performance. They offer a range of vibration welding machines designed to meet the diverse needs of different industries. Let's explore some of the key features and benefits of CEMAS vibration machines:
1. Hybrid Vibration Welders
CEMAS offers hybrid vibration welders that combine vibration welding with infrared preheating. This innovative approach softens the weld ribs before applying linear vibration, resulting in cleaner welds with reduced particulate flash. Hybrid vibration welding improves weld aesthetics and provides better control over the welding process.
2. Customizable Options
CEMAS vibration machines come with a wide range of customizable options to meet specific customer needs. With over 60 options available, you can tailor the machine to your exact requirements. This ensures that you get a vibration welding machine that fits your production processes perfectly.
3. World-Leading Components
CEMAS vibration machines are equipped with components from world-leading suppliers. This ensures the highest quality and reliability of the machines. Safety is a top priority, and CEMAS machines comply with international safety standards. Additionally, the use of high-quality components ensures prompt availability of spares worldwide.
4. Advanced Technology and Intuitive Interface
CEMAS vibration machines incorporate the latest-generation electronic components and feature an intuitive graphical interface. The interface allows for easy language selection, parameter adjustment, and user-configured I/O. This user-friendly design streamlines operation and reduces the learning curve for machine operators.
5. Efficient Loading and Unloading
CEMAS vibration machines are designed with efficiency in mind. The loading and unloading area is positioned close to the operator, minimizing strain and reducing loading distance. This design ensures smoother and more ergonomic operation, improving overall productivity.
6. Wide Range of Models
CEMAS offers a range of vibration machine models to cater to different application requirements. Whether you are welding small to medium-sized taillights, intake manifolds, or larger rear lamps and spoilers, there is a CEMAS vibration machine suitable for your needs. The machines are designed to deliver consistent and reliable welds for a wide range of part sizes and geometries.
7. Real-Time Tuning and Enhanced Welding Control
CEMAS vibration machines feature real-time tuning, allowing for continuous adjustment of the vibration frequency to match the resonating tool mass and application characteristics. This ensures optimal welding performance and improved weld quality. The machines also offer enhanced control over the welding process, with the ability to stop vibration in less than 50 ms for stronger and more homogeneous joints.
CEMAS vibration machines are known for their advanced technology, high-quality components, and exceptional performance. Whether you require small and efficient machines or larger models for more demanding applications, CEMAS offers a comprehensive range of vibration welding solutions to meet your specific needs.
Advantages of Hybrid Vibration Welding
Hybrid vibration welding, as offered by CEMAS, combines the benefits of vibration welding with infrared preheating. This hybrid approach offers several advantages over traditional vibration welding techniques. Let's explore these benefits in detail:
1. Improved Weld Aesthetics
One of the key advantages of hybrid vibration welding is the improvement in weld aesthetics. By preheating the weld ribs using infrared radiation, the material softens, resulting in cleaner welds with reduced particulate flash. This enhances the overall appearance of the welded parts, making them more visually appealing.
2. Reduction in Particulate Flash
Particulate flash formation is a common occurrence in vibration welding. However, with the addition of infrared preheating in hybrid vibration welding, the weld ribs are softened before the vibration process. This reduces the amount of particulate flash generated during welding, resulting in cleaner welds and reducing the need for post-weld flash removal.
3. Enhanced Control and Flexibility
Hybrid vibration welding provides enhanced control and flexibility in the welding process. The addition of infrared preheating allows for precise control over the amount and distribution of heat in the joint area. This enables better control over the melting and flow of the material, resulting in improved weld quality and consistency.
4. Stress Reduction and Improved Strength
The combination of vibration welding with infrared preheating can help reduce stress in the weld joint. By softening the material before the vibration process, the material can flow more smoothly, reducing the likelihood of stress concentrations in the weld. This can lead to improved joint strength and overall weld integrity.
Hybrid vibration welding offers significant advantages over traditional vibration welding techniques, making it an attractive option for applications that require improved weld aesthetics, reduced particulate flash, and enhanced control over the welding process.
Taking the Next Step
If you are considering vibration welding manufacturing for your project, it is important to conduct a feasibility study to evaluate the suitability and potential benefits of this technique. A feasibility study can help determine the specific parameters, tooling requirements, and potential challenges associated with your project.
At Xfurth Ltd, we offer free feasibility studies to assist you in the decision-making process. Our team of experts will work closely with you to understand your project requirements and provide insights and recommendations based on our extensive experience in plastic welding and joining systems.
To get started with your vibration welding manufacturing project or to learn more about our range of products and services, contact Xfurth Ltd today. Our dedicated team is ready to assist you in achieving efficient, reliable, and high-quality welds for your thermoplastic parts.
Additional Information
To learn more about vibration welding manufacturing, we invite you to visit our blog on our website. Our blog provides valuable insights, in-depth articles, and industry updates on plastic welding and joining technologies. Stay up-to-date with the latest advancements and trends in the field of vibration welding by following our blog.
Ready to get started? Contact our team at Xfurth Ltd to discuss your project requirements and discover how vibration welding manufacturing can benefit your manufacturing processes. We look forward to partnering with you to achieve your goals in plastic assembly.
Conclusion
Vibration welding manufacturing is a highly efficient and cost-effective method for joining thermoplastic parts. With its ability to produce strong, airtight welds, compatibility with most thermoplastics, and fast cycle times, vibration welding is a preferred choice for various industries. By understanding the advantages and disadvantages of vibration welding, considering the size of the components, exploring alternative bonding options, and selecting the right vibration welding machine, manufacturers can achieve reliable and high-quality welds for their thermoplastic parts. Xfurth Ltd, in partnership with CEMAS, offers a range of vibration welding machines and comprehensive support to help customers achieve their desired weld results. Contact Xfurth Ltd today to discover how vibration welding manufacturing can enhance your production processes and meet your project requirements.