Ultrasonic Welding for Non-Woven Fabric: A Revolution in Joining and Sealing
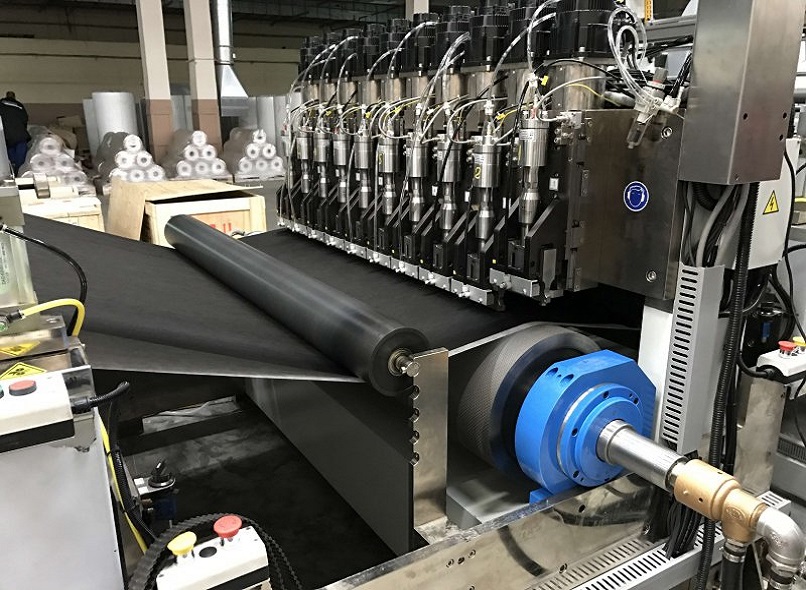
In the world of textile manufacturing, the demands for efficient and reliable methods of joining and sealing non-woven fabrics continue to grow. One innovative solution that has gained significant attention is ultrasonic welding. This technology offers numerous advantages over traditional bonding methods, such as adhesive-based techniques or sewing. Ultrasonic welding provides a clean and efficient way to join or slit synthetic materials, offering high precision, productivity gains, and eliminating the need for consumables. In this comprehensive guide, we will explore the ins and outs of ultrasonic welding for non-woven fabric, from its principles and applications to the benefits it offers and the latest advancements in the field.
1. Introduction to Ultrasonic Welding for Non-Woven Fabric
Understanding Ultrasonic Welding
Ultrasonic welding is a cutting-edge technology that has revolutionized the textile industry. It utilizes high-frequency sound waves to generate localized heat through vibration, causing thermoplastic fibers to bond together. Unlike traditional methods that rely on adhesives or sewing, ultrasonic welding offers a clean and efficient alternative, providing high precision and quality in joining non-woven fabrics. The process eliminates the need for consumables and adhesives, reducing production costs and avoiding potential product contamination. Ultrasonic welding also ensures a secure and durable bond, making it ideal for a wide range of textile applications.
The Significance of Non-Woven Fabric in Textile Manufacturing
Non-woven fabric is a versatile material that plays a crucial role in various industries, including medical, hygiene, consumer goods, and technical textiles. Unlike traditional woven fabrics, non-woven fabrics are created by bonding or entangling fibers together using mechanical, chemical, or thermal processes. This unique structure offers several advantages, such as enhanced breathability, liquid resistance, and ease of manufacturing. Non-woven fabrics are widely used in products like disposable medical gowns, diapers, filtration materials, and automotive components. The ability to efficiently join and seal non-woven fabrics is essential for ensuring the quality and performance of these products.
2. Applications of Ultrasonic Welding in the Textile Industry
Medical and Hygiene Products
In the field of medical and hygiene products, ultrasonic welding has become a preferred method for joining non-woven fabrics. The technology enables the production of contamination-resistant gowns, masks, and other non-woven fabric items used in healthcare settings. With ultrasonic welding, pleats and seals can be perfectly executed, meeting stringent regulatory requirements. The low-frequency options for high-speed, difficult-to-join welds allow for the bonding of multiple layers in products like medicated wipes, ensuring better effectiveness and purity.
Consumer Goods
Ultrasonic welding also finds extensive use in the manufacturing of consumer goods. Products such as diapers, mattress pads, absorbent household mops, premium auto seat covers, and leak-proof filter bags benefit from ultrasonic technology to create durable seals without the need for consumables or the risk of material damage. The versatility of ultrasonic welding makes it suitable for joining various non-woven fabrics used in everyday consumer products.
See more sonic welder for plastic