Introduction to Hot Plate Welding Equipment
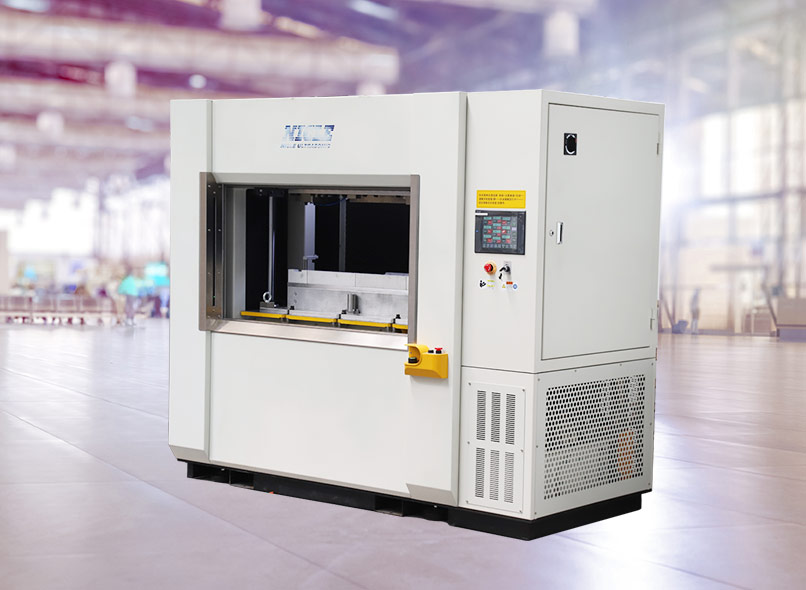
Hot plate welding equipment is a widely used thermal welding technique for joining thermoplastics. It offers the ability to create strong, hermetic, and durable welds in various applications. Whether it's large part assembly, pressure vessels, or automotive components, hot plate welding equipment provides precise control and reliability in the welding process.
In this comprehensive guide, we will explore the key aspects of hot plate welding equipment, including its working principle, advantages, applications, and different types of machines available in the market. We will also delve into the technical parameters, materials suitability, and the history of hot plate welding. So, let's dive in and discover the world of hot plate welding equipment.
1. What is Hot Plate Welding?
The Working Principle of Hot Plate Welding Equipment
Hot plate welding equipment utilizes a thermal welding technique to join thermoplastic parts. The process involves heating the joining surfaces of the parts using a heated platen, which is in contact or near proximity to the surfaces. The heat melts the thermoplastic material, and the parts are then pressed together under pressure to form a strong and durable bond.
Hot plate welding is a multi-stage process that includes matching, heating, change-over, and welding/forging phases. In the matching phase, the geometry of the weld surfaces is aligned to the theoretical welding plane. The heating phase involves heating the parts' surfaces until they reach a molten state. During the change-over phase, the parts are separated from the heated platen, and the platen is retracted. Finally, in the welding/forging phase, the molten surfaces are pressed together, allowing the material to cool and solidify under pressure, creating a strong weld.
The Advantages of Hot Plate Welding
Hot plate welding offers several advantages that make it a preferred choice for joining thermoplastic parts. Some of the key advantages include:
- Strong and Durable Welds: Hot plate welding creates welds with high strength and durability, often exceeding the strength of the parent materials.
- Hermetic Seals: The welding process can produce air-tight and leak-proof seals, making it suitable for applications requiring airtightness or liquid containment.
- Versatility in Part Design: Hot plate welding allows for the joining of parts with complex geometries, including those with contoured parting lines, internal walls, and free-standing walls.
- Reproducibility: The process provides consistent and reproducible welds, ensuring uniform quality in mass production.
- Material Compatibility: Hot plate welding is compatible with a wide range of thermoplastic materials, including polypropylene (PP), polyethylene (PE), PVC, and more.
Applications of Hot Plate Welding
Hot plate welding finds applications in various industries and product categories. Some common applications include:
- Automotive Industry: Hot plate welding is used for joining automotive components such as glove box covers, coolant tanks, sun visors, and air ducts.
- Pressure Vessels: Hot plate welding equipment is employed in the production of pressure vessels and pressure compensation vessels.
- Pipe Construction: Large-diameter plastic pipes can be effectively joined using hot plate welding, ensuring strong and reliable connections.
- Electronics and Electrical Engineering: Hot plate welding is utilized in the assembly of circuit boards and other electronic components.
- Household Technology: The process is employed in the production of household items like clean air pipes and appliance components.
The versatility and reliability of hot plate welding make it a preferred choice for industries requiring strong and durable welds in various thermoplastic applications.
2. Types of Hot Plate Welding Equipment
Hot plate welding equipment is available in different configurations to suit the specific requirements of various applications. The two main types of hot plate welding machines are vertical platen machines and horizontal platen machines. Additionally, there are semi and fully automated hot plate welding systems that offer increased productivity and efficiency.
Vertical Platen Hot Plate Welding Machines
Vertical platen hot plate welding machines are designed with a vertical orientation of the heating platen. These machines are manually loaded and unloaded, making them suitable for applications where precision alignment and control over the welding process are critical. The vertical configuration allows for easy access to the part halves during loading and unloading.
Horizontal Platen Hot Plate Welding Machines
Horizontal platen hot plate welding machines have a horizontally aligned heating platen. These machines are commonly used for parts with loose internal components or when automatic top-half part pick-up is necessary. The horizontal configuration facilitates the integration of automation systems, making it suitable for high-volume production environments.
Semi and Fully Automated Hot Plate Welding Systems
Semi and fully automated hot plate welding systems offer increased productivity and efficiency by integrating robotics and advanced control systems. These systems are designed for high-volume production and can perform tasks such as part loading, welding, and unloading automatically. They often incorporate features like automatic tool change systems and conveyor integration, enabling seamless production flow.
The choice between vertical or horizontal platen machines and the level of automation depends on the specific requirements of the application, production volume, and desired level of control and efficiency.
3. Hot Plate Welding Process
The hot plate welding process involves several stages, each crucial for achieving strong and reliable welds. These stages include the matching phase, heating phase, change-over phase, and welding/forging phase.
The Matching Phase
In the matching phase, the parts to be welded are securely held in position by precision holding fixtures. These fixtures ensure accurate alignment and support throughout the welding process. The weld surfaces are brought into contact with the heated platen to begin the heating process.
The Heating Phase
During the heating phase, the weld surfaces are heated through conduction by physical contact with the heated platen. The platen temperature is carefully controlled to reach the desired temperature range, typically above the melting temperature of the thermoplastic material. The heat transfers to the weld surfaces, causing them to soften and reach a molten state.
The Change-Over Phase
After the weld surfaces have reached the molten state, the parts are removed from the heated platen, and the platen is retracted. This phase, known as the change-over phase, allows the molten material to cool slightly while the parts are separated from the heat source. The duration of the change-over phase is minimized to prevent excessive cooling of the molten material.
The Welding/Forging Phase
In the final welding/forging phase, the molten surfaces of the parts are brought together under pressure. This pressure ensures proper bonding and allows the molten material to solidify and form a strong weld. The welding force is maintained until the joint cools and solidifies, ensuring a durable and reliable weld.
The hot plate welding process provides precise control over temperature, pressure, and time, resulting in consistent and high-quality welds.
4. High-Temperature Hot Plate Welding
High-temperature hot plate welding is a variant of the conventional hot plate welding process. It involves using an uncoated hot plate heated to temperatures between 300 and 400 °C (572 and 752 °F). The high temperature reduces the viscosity of the molten material, allowing it to peel off from the hot plate when removing the parts. This variant is particularly useful when working with materials that tend to stick to the hot plate surface, ensuring clean and reliable welds.
High-temperature hot plate welding offers advantages such as increased process control and reduced cycle times. It is commonly employed in applications where materials require higher temperatures for effective welding, or when the material tends to adhere to the hot plate surface.
5. Non-Contact Hot Plate Welding
Non-contact hot plate welding is another variant of hot plate welding that offers unique benefits in certain applications. In non-contact hot plate welding, temperatures higher than 900 °F are used, which allows for precise control of the heat without the need for physical contact between the heated platen and the parts being welded. This technique is particularly suitable for parts with complex geometries or those that cannot be easily accessed by a traditional hot plate.
Non-contact hot plate welding eliminates the risk of material sticking to the hot plate and provides highly controlled heat application. However, it typically requires longer cycle times compared to other hot plate welding techniques and is more complex to implement.
Non-contact hot plate welding is used in specialized applications where precise heat control and weld quality are crucial. It offers advantages in situations where physical contact between the hot plate and the parts is not feasible or desirable.
6. Materials Suitable for Hot Plate Welding
Hot plate welding is compatible with a wide range of thermoplastic materials, making it a versatile welding technique. Some of the commonly used thermoplastics suitable for hot plate welding include:
- Polypropylene (PP)
- Polyethylene (PE)
- PVC (Polyvinyl Chloride)
- ABS (Acrylonitrile Butadiene Styrene)
- PA (Polyamide)
- PC (Polycarbonate)
- PMMA (Polymethyl Methacrylate)
Each material has its own melting temperature and melt characteristics, which need to be considered when determining the appropriate hot plate welding parameters. The choice of material depends on the specific application requirements, including mechanical properties, chemical resistance, and environmental conditions.
Hot plate welding offers the advantage of being compatible with a wide range of materials, allowing for flexibility in design and material selection.
7. Factors Affecting Hot Plate Weld Quality
Several factors contribute to the quality and strength of hot plate welds. Controlling these factors is crucial to ensure consistent and reliable welds. The key factors affecting hot plate weld quality are temperature control, time control, pressure control, and force control.
Temperature Control
Temperature control is critical in hot plate welding to ensure proper melting of the thermoplastic material. The temperature of the heated platen should be set within the appropriate range for the specific material being welded. Precise temperature control helps achieve consistent weld quality and minimizes the risk of material degradation or overheating.
Time Control
The heating and cooling times during the hot plate welding process should be carefully controlled to achieve optimal weld quality. The heating time determines the duration for which the weld surfaces are exposed to the heated platen, allowing them to reach the desired molten state. Similarly, the cooling time allows the molten material to solidify and form a strong bond. Proper time control ensures uniform welds and prevents under or overwelding.
Pressure Control
Applying the correct pressure during the welding/forging phase is crucial for achieving strong and durable welds. The pressure ensures proper contact between the molten surfaces and promotes molecular diffusion and entanglement of the plastic molecules. The pressure applied should be sufficient to create a strong bond but not excessive to avoid material deformation or cold welds.
Force Control
Force control is particularly important in hot plate welding equipment with twin motion fixturing, where independent control of force and speed is available for each part half. This allows for precise control over the welding process, ensuring uniform force distribution and optimal material flow during the welding/forging phase. Proper force control helps achieve consistent weld strength throughout the joint.
By effectively controlling temperature, time, pressure, and force, manufacturers can ensure high-quality welds with consistent strength and durability.
8. History of Hot Plate Welding
Hot plate welding has a rich history, dating back to the early 1930s when it was first used for joining PVC. Over time, the technique gained popularity with the increasing use of polyolefins, which are challenging to bond using adhesives. By the 1960s, hot plate welding had become one of the most widely used plastic welding methods.
Hot plate welding found applications in various industries, including pipeline construction, appliances, and injection moldings. National and international associations for welding, such as the Deutscher Verband fuer Schweissen (DVS), the American Welding Society (AWS), and the Comité Européen de Normalisation (CEN), developed specifications and guidelines for hot plate welding.
Advancements in technology and process optimization have further improved the quality and efficiency of hot plate welding, making it a trusted and widely used technique for joining thermoplastics.
9. Inspection Techniques in Hot Plate Welding
Ensuring the quality of hot plate welds is crucial to meet the required standards and performance characteristics. Various inspection techniques are implemented to identify discontinuities or defects in the welds. These techniques help manufacturers assess the integrity and reliability of the welds and take corrective actions if necessary.
Some commonly used inspection techniques in hot plate welding include:
- Visual Inspection: Visual examination of the welds to detect any visible defects, such as uneven surfaces, voids, or flash.
- Non-Destructive Testing (NDT): NDT techniques, such as ultrasonic testing and X-ray inspection, can be used to detect internal defects or discontinuities that may not be visible to the naked eye.
- Destructive Testing: Destructive testing involves taking samples of the welded parts and subjecting them to various mechanical tests, such as tensile testing or peel testing, to assess the weld strength and integrity.
Implementing comprehensive inspection techniques ensures that hot plate welds meet the required quality standards and perform reliably in their intended applications.
10. Advancements in Hot Plate Welding Equipment
Advancements in hot plate welding equipment have contributed to improved efficiency, precision, and reliability in the welding process. Manufacturers have developed innovative solutions and incorporated advanced technologies to meet the evolving needs of various industries.
Some of the advancements in hot plate welding equipment include:
- Enhanced Temperature Control: Modern hot plate welding machines feature precise temperature control systems, allowing for accurate and consistent temperature profiles during the welding process.
- Automation and Robotics: Semi and fully automated hot plate welding systems integrate robotics and advanced control systems to optimize productivity and reduce labor costs. These systems can perform tasks such as part loading, welding, and unloading with minimal human intervention.
- Improved Tooling and Fixturing: Advanced tooling and fixturing technologies provide precise alignment and positioning of the parts during the welding process, ensuring consistent weld quality.
- Process Monitoring and Data Logging: Hot plate welding equipment now includes advanced monitoring systems that capture process parameters, such as temperature, pressure, and time, allowing for real-time monitoring and analysis of the welding process. This data can be used for quality control and process optimization.
These advancements have made hot plate welding equipment more reliable, efficient, and adaptable to various application requirements. Manufacturers can benefit from increased productivity, improved weld quality, and reduced cycle times.
11. Choosing the Right Hot Plate Welding Equipment
Selecting the appropriate hot plate welding equipment is crucial to ensure optimal performance, precision, and efficiency in the welding process. Several factors should be considered when choosing hot plate welding machines, including:
- Application Requirements: Assess the specific requirements of the application, including the size and complexity of the parts, production volume, and desired weld quality.
- Material Compatibility: Consider the thermoplastic materials to be welded and ensure that the selected equipment is compatible with those materials.
- Machine Configuration: Evaluate the available options, such as vertical or horizontal platen machines, and determine the most suitable configuration based on the application's needs.
- Automation Capability: If automation is desired, consider the level of automation offered by different hot plate welding systems and select one that aligns with production requirements.
- Process Control and Monitoring: Assess the machine's capabilities for temperature, pressure, and time control, as well as data logging and process monitoring features.
- Reliability and Support: Consider the reputation and track record of the equipment manufacturer, as well as the availability of technical support and after-sales service.
By carefully evaluating these factors, manufacturers can choose the right hot plate welding equipment that meets their specific requirements and ensures optimal weld quality and productivity.
12. Conclusion
Hot plate welding equipment offers a reliable and efficient solution for joining thermoplastic parts. With its ability to produce strong, hermetic, and durable welds, hot plate welding has found widespread applications in various industries. The precise control over temperature, pressure, and time ensures consistent weld quality and performance.
Advancements in hot plate welding technology, such as enhanced temperature control, automation, and process monitoring, have further improved the efficiency and reliability of the welding process. Manufacturers can benefit from increased productivity, improved weld quality, and reduced cycle times.
Choosing the right hot plate welding equipment involves considering factors such as application requirements, material compatibility, machine configuration, automation capability, and process control features. By selecting the appropriate equipment, manufacturers can achieve optimal weld quality and efficiency in their production processes.
Hot plate welding equipment continues to evolve, driven by the need for stronger, more reliable welds in a wide range of thermoplastic applications. As technology advances, hot plate welding will remain a key welding technique, offering versatility, precision, and durability in joining thermoplastics.
See more hot plate welding